Optimising Surface Quality
Innovative Roughness and Waviness Measurement with EMG SORM®
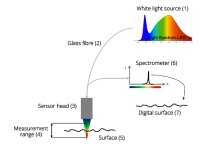
(PresseBox) - The steel, aluminium and automotive industries require strict control over surface characteristics to ensure product quality, process efficiency, and overall durability. Surface roughness and waviness directly affect coating adhesion, visual appearance, and structural integrity. In response to these stringent demands, EMG has introduced the latest generation of its EMG SORM® system, offering an innovative approach to online roughness and waviness measurement based on the confocal chromatic principle. This article explores the working principle, system architecture, and seamless integration of this cutting-edge technology into production lines.
Advanced Surface Measurement with the Confocal Chromatic Principle
Traditional roughness measurement methods rely on tactile stylus instruments, which, while precise, are impractical for continuous in-line measurement. The challenge becomes even more pronounced when assessing surface waviness, where traditional methods often fall short in terms of accuracy and efficiency. The confocal chromatic principle addresses these limitations through advanced optical technology. In the measurement process, a white light source (1) emits a broad spectrum of wavelengths. This light is transferred by a glass fibre cable (2) and passed through the sensor head (3), which contains a chromatic lens system. The lenses disperse the different wavelengths along the optical axis. Each wavelength is focused on a different point, creating a series of focal points along the measurement range (4). The optical system is positioned above the strip surface (5) to be measured. As the system scans across the surface, different wavelengths are focused on the surface depending on the surface profile height].
When a specific wavelength s focal point coincides with the surface, that wavelength is reflected back through the lens system. A spectrometer (6), positioned to only receive light from the exact focal plane, captures the reflected light. The spectrometer is sensitive to the wavelength of the reflected light, determining the exact distance from the lens to the surface at that point. As the system scans over the surface, it continuously measures the distance to the surface at various points, capturing a high-resolution profile of the surface topography and creates a digital surface (7). This data is then processed to calculate surface roughness parameters (such as Ra and RPc) and waviness.
This technique provides several key advantages. It features:
non-contact measurement, meaning that unlike stylus-based systems, confocal chromatic technology does not physically touch the surface,
operations at production speeds up to 350 m/min for roughness and for waviness measurement, ensuring seamless integration into modern high-speed production lines, and
offering reliable accuracy in real-time, achieving an accuracy of±15 % for roughness values and waviness parametres as well as ±20 % for peak count (RPc) values for strip speeds up to 230 m/min, making it a reliable solution for quality control.
System Architecture and Operational Integration
The new EMG SORM® system is engineered to be robust and flexible, ensuring seamless deployment into existing production lines. It consists of the following key components: a measurement head, mounted on an electromotive traversing unit, which scans the steel strip at various positions while maintaining a fixed measuring distance of 25 mm from the strip surface to ensure precise data capture without interference from vibrations or height fluctuations. The evaluation controller processes raw measurement data and converts it into meaningful roughness and waviness parameters, operating within a standard industrial PC (IPC) housed inside a control cabinet. The traversing unit ensures that the measuring head can scan the entire strip width, providing a surface profile over coil width and length. The visualization terminal, located in the control room, features a graphical user interface (GUI) that enables real-time monitoring and analysis of measurement data, offering production engineers valuable insights for process optimisation. The system also includes a communication system that integrates seamlessly with industrial networks using Ethernet or Profibus DP, ensuring smooth data exchange with existing control infrastructures. The EMG SORM® system is designed for minimal space requirements, making it ideal for a wide range of applications, including continuous galvanising lines (CGL), electrolytic galvanising lines (EGL), and automotive blanking lines in steel, aluminum and stainless-steel production. Additionally, it supports various surface structures such as EBT, EDT, LBT, SBT, and PRETEX® without the need for recalibration.
Seamless Integration into the Production Line
One of the most critical aspects of any measurement system is its ability to integrate efficiently into production environments. The EMG SORM® system achieves this through several key features. Its compact design, with a space requirement of less than 400 mm in the production direction, allows for easy installation in most production facilities. Unlike laser-based measurement systems, it has no special safety requirements, simplifyingits implementation. Furthermore, the system allows strip thickness variations of up to 3 mm without the need of vertical movement of the sensor head. In other cases it can be equipped with an automatic refocusing unit.
For the first time, this system measures both roughness and waviness using a single sensor, unlike previous known systems that required separate measurement solutions.
Looking Ahead
The EMG SORM® system represents a significant advancement in online roughness and waviness measurement, combining precision, speed, and ease of integration in one sensor. This innovative approach enables manufacturers to maintain high surface quality, optimise production processes, and ensure compliance withstringent industry standards. While this article has focused on the technical foundation and integration of the system, the next article will delve into the measurable benefits and results of its implementation. Stay tuned for a detailed analysis of the results and their impact on modern steel production.
For support and further details on how the EMG SORM® system can enhance your production processes, contact EMG Automation GmbH, or reach out to our product manager, Franziska Kneisel, for detailed information and support.
Bereitgestellt von Benutzer: PresseBox
Datum: 26.03.2025 - 10:50 Uhr
Sprache: Deutsch
News-ID 2161351
Anzahl Zeichen: 0
Kontakt-Informationen:
Ansprechpartner: Claudia Schreiner
Stadt:
Wenden
Telefon: +49 (2762) 612-282
Kategorie:
Industrietechnik
Dieser Fachartikel wurde bisher 71 mal aufgerufen.
Der Fachartikel mit dem Titel:
"Optimising Surface Quality"
steht unter der journalistisch-redaktionellen Verantwortung von
elexis AG (Nachricht senden)
Beachten Sie bitte die weiteren Informationen zum Haftungsauschluß (gemäß TMG - TeleMedianGesetz) und dem Datenschutz (gemäß der DSGVO).