Innovation braucht Kreativität
Rückblick auf die INFRAROT Konferenz 2010 in Hamburg
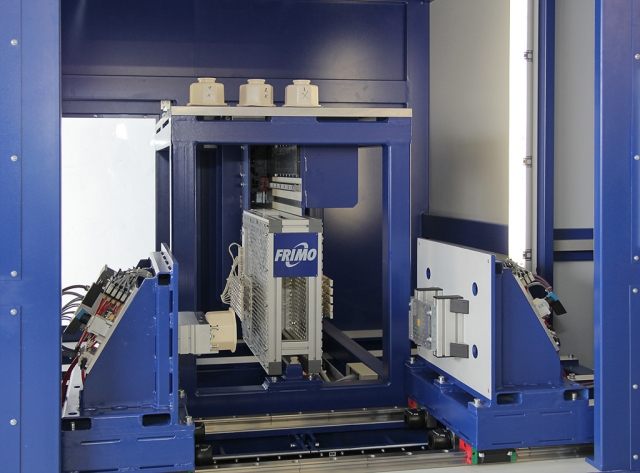
(IINews) - LOTTE / HAMBURG "Innovation braucht Kreativität - Wissen multiplizieren statt addieren" - unter diesem Motto trat am 17. und 18. Juni 2010 die Kunststoffbranche in Hamburg zusammen. Mehr als 60 Teilnehmer aus ganz Deutschland besuchten die Veranstaltung, um auf Initiative des Gastgebers FRIMO Technology GmbH über aktuelle Entwicklungen und Perspektiven beim Infrarotschweißen zu diskutieren. Stark vertreten war die Automobilbranche mit Experten von Audi, BMW und VW sowie zahlreichen Teilnehmern von Tier 1 suppliern wie unter anderem Carcoustics, Faurecia, Fehrer, IAC, Johnson Controls, Mann & Hummel, Magna, MöllerTech, Rieter und Röchling. Ebenso waren mit Firmen wie Brita, Hauni, Rehau und Stihl auch Spezialisten für verschiedenste technische Kunststoffanwendungen, bei denen Fügeprozesse gefragt sind, vor Ort.
Ein gemeinsamer Blick über die gesamte Wertschöpfungskette, Darstellungen zum Stand der Technik, der Austausch von best practices, Updates über neueste wissenschaftliche Erkenntnisse sowie die Erarbeitung von Zukunftsperspektiven und damit verbunden die Initiierung gemeinsamer Projekte waren die Ziele der Veranstaltung. Begleitet durch Vorträge von Herstellern und Anwendern bot die zweitägige INFRAROT Konferenz ein breites Informationsspektrum über den Umgang mit dieser erfolgversprechenden Technologie. Abgerundet wurde das Branchentreffen durch Technologie Live-Vorführungen am FRIMO Standort in Hamburg. Präsentiert wurden die neuen FRIMO JoinLine Serien- und Laboranlagen JoinLine IR-H "Highspeed" und JoinLine IR-V. Darüber hinaus wurden das robotergestützte Schweißen ebenso wie Material- und Schweißversuche sowie weitere Fügeverfahren live vor Ort demonstriert.
Alte Wege verlassen, um neue Ziel zu erreichen:
"Informationen austauschen, um Anregungen zu bekommen - das war das Ziel, welches wir erfolgreich umgesetzt haben. Detlev Böl, Geschäftsleitung der FRIMO Technology GmbH zeigte sich zum Veranstaltungsende mehr als zufrieden. "Wir haben mit der INFRAROT Konferenz eine neutrale Plattform geschaffen, die es ermöglicht, mit der gesamten Branche zu diskutieren." Hersteller und Anwender sollten das Infrarotschweißen besser kennenlernen und beurteilen können. Die Technologie stand ganz klar im Vordergrund. FRIMO selbst hat sich als Maschinenhersteller der Diskussion gestellt, um gemeinsam über zukünftige Lösungen zu sprechen und weitere konstruktive Verbesserungen auf den Weg zu bringen.
Partikelsauberkeit als Qualitätsmerkmalmerkmal:
Das Thema Sauberkeit hat sich in der Kunststoffbranche zu einem immer wichtiger werdenden Qualitätsmerkmal entwickelt. In der Automobil- und Zulieferindustrie ebenso wie bei Hydraulik-Komponenten, in der Medizintechnik, Reinigungstechnik, Feinwerktechnik, in der Luft- und Raumfahrttechnik und vielen weiteren Bereichen werden verschiedene Prüfverfahren zur Feststellung der Bauteilsauberkeit angewandt. Volker Burger, Geschäftsführer der CleanControlling GmbH, beschäftigt sich mit der Durchführung von Restschmutzanalysen bzw. Sauberkeitsanalysen gemäß ISO 16232, VDA 19, ISO 4405/4406 sowie den individuellen Werksnormen. Sein fundiertes Wissen aufgrund langjähriger Erfahrung im Bereich Technische Sauberkeit nutzte er während der INFRAROT Konferenz in Hamburg für einen Vortrag zum Thema Normen, Restschmutz und Partikelverordnungen und ihre Auswirkungen in der Praxis. Sein Fazit zum Infrarot-Thema: "Partikelsauberkeitsanforderungen haben sich zu einem anerkannten Zeichnungsmerkmal ähnlich einem Maßeintrag entwickelt. Die Partikelentwicklung in den Fertigungsprozessen ist von großer Bedeutung und hier haben Fügeprozesse, die systembedingt eine geringe Partikelentwicklung aufweisen, einen großen Vorteil. Das Infrarotfügen erfüllt diese Voraussetzung in sehr guter Weise." Weitere Infos unter: http://www.cleancontrolling.de
Infrarotschweißen sorgt für Idealvoraussetzungen:
Michael Goos, Technical Marketing Manager von Ticona, beleuchtete in Hamburg die Infrarot-Technologie aus Sicht eines Herstellers von langfaserverstärkten Kunststoffen. Nach mehreren Untersuchungen kristallisierten sich für Ticona deutlich die Vorteile von Infrarot gegenüber dem bisherigen Vibrationsschweißverfahren heraus. Ein höheres Zähigkeitspotenzial sowie die höhere Festigkeit deuten für Goos eindeutig auf die effektivere Schweißverbindung durch Infrarot hin: "Das Verfahren ermöglicht Idealvoraussetzungen bei Steifigkeit und Zähigkeit." Auch im direkten Vergleich mit dem Ultraschallschweißen gewinnt nach Ansicht von Goos die Infrarottechnik: "Ausgehend von gleichen Basismaterialien können hinsichtlich Zugkraft und Zugdehnung bessere Werte erzielt werden, was sich im Automotive-Bereich beispielsweise essentiell auf das Crashverhalten auswirkt. Darüber hinaus sind die Schweißnähte beim Infrarotschweißen sauberer als beim Ultraschallschweißen. Unsere Schweißuntersuchungen am langfaserverstärkten Thermoplast Celstran PP wiesen weder Störstellen am Bauteil noch optische Fehler auf." Weitere Infos unter: http://www.ticona.de
Infrarottechnologie ins rechte Licht rücken:
Die Heraeus Noblelight GmbH entwickelt und produziert Infrarot-Strahler und Systeme für industrielle Wärmeprozesse im Bereich Industrielle Prozesstechnik. Dieser Heraeus-Konzernbereich gehört weltweit zu den Markt- und Technologieführern für Speziallampen und Module im Wellenlängenbereich von Ultraviolett bis Infrarot für industrielle, wissenschaftliche und medizinische Anwendungen. Anwendungsberater Dr. Thomas Spendel referierte in seinem Vortrag zum Thema "Infrarot-Strahler - Technologie, Aufbau und Handhabung." In der Zusammenfassung seines Vortrages machte Spendel deutlich, dass insbesondere kurzwellige Infrarot-Strahler eine hohe Leistung mit hoher Tiefenwirkung kombinieren, wodurch sie eine hohe Produktivität gewährleisten. "Das schnelle Ein- und Ausschalten kurzwelliger Infrarot-Strahler spart Energie und ermöglicht sichere Prozesse. Darüber hinaus können 3-D-Teile mit konturangepassten Infrarot-Strahlern erwärmt werden," so Spendel. "Um den richtigen Strahler für ihren Anwendungsprozess zu finden, ist Abstimmung erforderlich: Die Wellenlänge muss perfekt auf das Material abgestimmt werden, die Strahler müssen optimal zur Anlage passen und die Leistung wiederum muss optimal an den Prozess angepasst werden." Weitere Infos unter: http://www.heraeus-noblelight.com
Zeit, Geld, Qualität - die neuen JoinLine Infrarotanlagen von FRIMO:
Einen praxisorientierten Überblick über neueste Entwicklungen von Infrarot-Standardfügeanlagen und -werkzeugen bot Helge Barkhoff vom Vertrieb der FRIMO Technology GmbH. Er machte deutlich, wie sehr sich im heutigen Wirtschaftsleben die Faktoren Zeit, Geld und Qualität auf die Produktion auswirken und zeigte auf, welche Konsequenzen sich daraus für die Entwicklung neuer Anlagen für das Infrarotfügen ergeben. Die strikten Voraussetzungen der Anwenderindustrie nahm Barkhoff als Anlass zur detaillierten Vorstellung der beiden neuen Anlagenserien aus dem Hause FRIMO: FRIMO JoinLine IR-H "Highspeed" und FRIMO JoinLine IR-V. Beide Anlagen erlauben schnelle Taktzeiten und überzeugen bei durchschnittlich fünfminütigem Werkzeugwechsel von der Vorder- oder Hinterseite der Anlage durch Schnelligkeit und Flexibilität. Darüber hinaus zeichnen sich die Serien durch eine hohe Anlagenverfügbarkeit und eine optimale Prozesssicherheit während der Produktion aus.
Weitere Infos unter: http://www.frimo.com.
Mit individuellen Lösungen zum Ergebnis:
Lösungen für mehr Produktivität präsentierte Uwe Krause von der Geschäftsleitung der FRIMO Technology GmbH. Sein Vortrag "Sonderbauformen Infrarotschweißanlagen und robotergestützte Anwendungen" befasste sich anhand dreier Beispiele zunächst mit Kombianlagen für Infrarot- und Ultraschallschweißen für die Instrumententafelfertigung im Automotive-Bereich, anschließend mit Wechselanlagen und im dritten Beispiel mit einer High-Speed-Infrarotanlage für schnelles und flexibles Infrarotschweißen. Last but not least widmete sich Krause Roboteranwendungen, wobei er auf robotergestütztes Schweißen, modular aufgebaute und flexible Roboterzellen sowie Multi-Funktions-Zellen zu sprechen kam. Auch Krause unterstützte die einhellige Meinung seiner Vorredner, indem er der technischen Spezifikation eines Projektes immer eine Ergebnisdefinition voranstellte: "Um das optimale Maschinenkonzept zu erarbeiten, sind die projektspezifischen Anforderungen zu definieren." Weitere Infos unter: http://www.frimo.com
Einfache und präzise Anlagensteuerung:
"Alles unter Kontrolle" - mit diesem geflügelten Wort übernahm Thorsten Geldmacher, Leiter Steuerungstechnik der FRIMO Technology GmbH, das Wort und lenkte den Fokus auf die Kompetenzbereiche Steuerung, Überwachung und Dokumentation. Geldmacher machte deutlich, wie sehr die unterschiedlichen Konturen und Materialien der zu verschweißenden Bauteile für eine Vielzahl an beachtenswerten Parametern sorgen. "Schmale und breite Fügezonen, Materialiendiversitäten, Sichtkanten, übereinander gelagerte Strahler, variierende Materialstärken - wer wirklich alles unter Kontrolle haben möchte, muss sich im Klaren darüber sein, all diese Parameter nicht nur zu beachten, sondern zielführend zu steuern." Als Lösung präsentierte Geldmacher einen Ausblick auf die neue FRIMO-Steuerung - eine flexibel anpassbare und modular erweiterbare All-In-One-Lösung für Steuerung, Überwachung und Dokumentation. Weitere Infos unter: http://www.frimo.com
Infrarot schafft Sicherheit in der Bildverarbeitung:
Interessante Ansätze bot die INFRAROT Konferenz ebenfalls in Bezug auf die Bildverarbeitung. Michael Wandelt, Geschäftsführer der AT - Automation Technology GmbH ist Spezialist auf dem Gebiet der 3D-Bildverarbeitungsprodukte sowie Spezialist für die Infrarot-Bildverarbeitung und die zerstörungsfreie Prüfung. Wandelt lieferte im Zuge der INFRAROT Konferenz Einblicke in seine Arbeit und referierte über den Einsatz der Infrarot-Bildverarbeitung für die Prozesskontrolle und Qualitätssicherung in der Kunststoffverarbeitung. Insbesondere widmete sich Wandelt dabei den Themen Temperaturüberwachung sowie Lunkerdetektion durch den Einsatz der Infrarottechnologie. Typische Anwendungsgebiete sind Qualitätskontrollen an Interieur-Bauteilen von Kraftfahrzeugen, Thermoelastische Spannungsanalyse (TSA), Prüfung von Bauteilen aus Faserverbundwerkstoffen, Untersuchung auf verborgene Defekte, Risse und Delaminationen in Bauteilen aus Kunststoff oder Metall, Beurteilung von Schweißnähten, Löt-, Niet-, und Klebeverbindungen. Weitere Infos unter: http://www.automationtechnology.de
Qualität beginnt mit der richtigen Auswahl der Fügetechnologie:
Dipl.-Ing. Reinhild Hoffschlag von der Universität Paderborn im Fachgebiet Kunststofftechnik ist vom Potenzial der Infrarottechnologie überzeugt, warnt jedoch gleichzeitig vor einem allzu großen Hype. Sie rät deshalb bewusst zu fundierter Grundlagenforschung. Für sie beginnt das Problem bereits oftmals in der Auswahl des passenden Werkstoffs: "Jeder Werkstoff hat unterschiedliche Schweißeigenschaften. Für die Anwender ist es deshalb manchmal schwierig, einem bestimmten Werkstoff das optimale Schweißverfahren zuzuordnen. Insbesondere dann, wenn das präferierte Verfahren und oder das präferierte Material nicht über aussagekräftige Erfahrungswerte verfügt. Die Anforderungen an das Produkt oder dessen Baugruppen sollten bereits in der Planungsphase konkret definiert und die dazugehörige Prüfmethode festgeschrieben werden." Hoffschlag rief deshalb dazu auf, sich intensiver mit den Verfahrensanalysen zu beschäftigen, insbesondere beim Schweißen niederviskoser Thermoplaste, wie sie häufig für die Automobilindustrie verwendet werden. Ferner verwies sie auf die wichtigen Beziehungen zwischen der Industrie sowie den Verbänden und Hochschulen und ermutigte die Beteiligten, sich in allseitigem Interesse zukünftig vermehrt auszutauschen. Die angestrebte Richtlinienarbeit des DVS (Deutscher Verband für Schweißen und verwandte Verfahren e.V.) könnte hierfür ein erster Ansatz sein und wichtige Grundlagen schaffen. Zudem ermahnte Hoffschlag die Anwesenden, für alle Eventualitäten die Ursache im Fügeprozess zu suchen und führte aus: "Die Fügetechnik ist häufig einer der letzten Produktionsschritte bei der Bauteilherstellung. Es darf nicht alleine ihre Aufgabe sein, sämtliche Qualitätsschwankungen vorangegangener Prozessschritte auszugleichen. Weitere Infos unter: http://www.ktpweb.de
Die letzen sind die Schweißer:
"Schweißer können viel, aber sicher nicht alles", meinte auch Otto Marquardt, Leiter Pre-Engineering der FRIMO Technology GmbH, und spielte damit auf die Position der Schweißer innerhalb der Prozesskette an. Sein Vortrag titelte mit dem Thema "Bauteil- und Schweißnahtgeometrien - Intelligente und kostenoptimierte Werkzeugauslegung". Die frühzeitige Einbindung eines Fügespezialisten sei essentieller Bestandteil für optimale Schweißergebnisse. Die Vorfertigung müsse berücksichtigt werden, ebenso wie Toleranzen und sonstige Abweichungen. Er ging während des Vortrags gezielt auf den Begriff der Fügezonen ein und erläuterte die Besonderheiten bei deren Auslegung in den unterschiedlichen Schweißverfahren. Darüber hinaus veranschaulichte er anhand von Versuchsreihen den Einfluss von Heizzeit und Fügedruck auf die Schweißnahtfestigkeit, die sich mit Hilfe von Handmustern der unterschiedlichsten Materialkombinationen veranschaulichen ließen. Marquardt resümierte: "Das Endprodukt muss frühzeitig definiert werden, um daraus das optimale Fügeverfahren abzuleiten. Im Rückschluss können die frühzeitig kommunizierten Fügevorhaben bereits in der Konstruktion Berücksichtigung finden." Weitere Infos unter: http://www.frimo.com
Fazit:
Mit der INFRAROT Konferenz in Hamburg wurde am 17. und 18. Juni ein transparentes Forum geschaffen, auf dem Hersteller und Anwender die Möglichkeit fanden, sich ausgiebig auszutauschen, Probleme zu beschreiben und Lösungen zu diskutieren, um daraus Vorteile für eigene Projekte zu erkennen. Man darf gespannt sein auf die kommenden Entwicklungen in dieser aktuellen und erfolgversprechenden Technologie und damit auf eine kontinuierliche Fortführung der INFRAROT Konferenz. Weitere Infos unter http://www.frimo.com. Videomaterial zur INFRAROT Konferenz unter http://www.kunststoffe.tv/de
Themen in diesem Fachartikel:
Unternehmensinformation / Kurzprofil:
Die FRIMO Unternehmensgruppe gehört zu den weltweit führenden Herstellern von Systemlösungen zur Fertigung hochwertiger Kunststoffkomponenten. Zur FRIMO Unternehmensgruppe gehören weltweit 15 Standorte mit über 1.000 Mitarbeitern sowie zahlreiche internationale Vertretungen. Die Gruppe konnte trotz schwierigem Marktumfeld in 2009 einen Auftragseingang von mehr als 130 Mio. Euro erzielen und wurde wiederholt für herausragende Leistungen, z.B. mit dem SPE Award, ausgezeichnet. Das Angebot von FRIMO für die Kunststoff verarbeitende Industrie reicht von den unterschiedlichsten Verfahren zur PUR-Verarbeitung über das Flexible Schneiden, Stanzen, Pressen und Formen sowie Thermoformen, Kaschieren und Umbugen bis hin zu Füge- und Klebeprozessen. FRIMO bietet seinen Kunden hierfür maßgeschneiderte Werkzeuge, Maschinen und Anlagen als Einzel- oder Komplettlösung aus einer Hand.
WIRKSTOFFGRUPPE GmbH
Michael Mücher
Am Zollstock 11
57439
Attendorn
m.muecher(at)wirkstoffgruppe.de
02722639926
http://www.wirkstoffgruppe.de
Datum: 19.07.2010 - 13:47 Uhr
Sprache: Deutsch
News-ID 230129
Anzahl Zeichen: 0
Kontakt-Informationen:
Ansprechpartner: Martina Schierholt
Stadt:
Lotte
Telefon: +49 (05404) 886-157
Kategorie:
Maschinenbau
Anmerkungen:
Dieser Fachartikel wurde bisher 1284 mal aufgerufen.
Der Fachartikel mit dem Titel:
"Innovation braucht Kreativität"
steht unter der journalistisch-redaktionellen Verantwortung von
FRIMO Group Marketing (Nachricht senden)
Beachten Sie bitte die weiteren Informationen zum Haftungsauschluß (gemäß TMG - TeleMedianGesetz) und dem Datenschutz (gemäß der DSGVO).