„Der Kern ist die Vermeidung von Verschwendung“
Interview mit Ulrich Fröleke von Treston zu Kritik an Lean Production
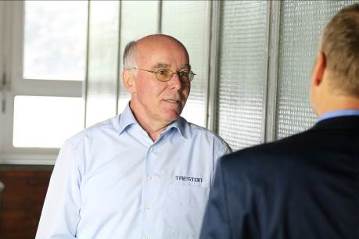
(IINews) - Lean Production im Unternehmen einzuführen, klingt nach vielen Vorteilen: effizientere Produktionsabläufe, strukturiertere Materialzufuhr, reduzierte Lieferzeiten, mehr Teamarbeit, weniger hierarchischer Aufbau. Tatsächlich begegnen Treston Deutschland bei der Beratung von Industrieunternehmen zur Einführung von Lean-Prinzipien viele Vorbehalte und Gegenargumente. Was steckt dahinter? Ulrich Fröleke, Lean-Experte bei Treston, hinterfragt im folgenden Interview häufige Vorurteile gegen Lean Production und zeigt auf, wie jedes Unternehmen von Lean-Strukturen profitieren kann.
Herr Fröleke, ist Lean Production für jeden Betrieb geeignet? Die Kritik lautet häufig, dass die Verhältnisse der japanischen Automobilindustrie nicht einfach auf andere Länder und Industriezweige übertragbar seien.
Fröleke: Man kann die Lean-Philosophie letztlich auf einen zentralen Aspekt herunterbrechen: Vermeidung von Verschwendung. Unabhängig davon auf welcher Ebene, in welcher Funktion, ob es sich um Material, Fläche oder menschliche Ressourcen handelt, der Kern ist die Vermeidung von Verschwendung. Und dieser zentrale Gedanke lässt sich auf jeden produzierenden Betrieb anwenden – und sollte auch immer im Interesse der Verantwortlichen vor Ort liegen. Wie man diesen Ansatz ausgestaltet, muss immer individuell für jedes Unternehmen entschieden werden.
Was entgegnen Sie Kritikern?
Fröleke: Das kommt darauf an, aus welcher Richtung die Kritik oder die Vorurteile kommen. Es gibt viele wissenschaftliche Abhandlungen über das Für und Wider der Lean Production. Das wirkt aber eher nebulös und wenig konkret. Tatsächlich muss man sich die praktische Seite vor Ort in jedem einzelnen Betrieb anschauen. Und dann mit den Bedenken der Verantwortlichen und Mitarbeiter vor Ort umgehen. Wenn wir über Kritik an Lean Production sprechen, würde ich gerne die Argumente gegen Lean Production, die direkt aus den Unternehmen kommen und die mir regelmäßig in unseren Beratungen begegnen, einmal aufzeigen – und diese dann widerlegen. Denn in den meisten Fällen sind Bedenken unbegründet, man muss das Projekt „Lean“ nur richtig angehen.
Was sind denn die häufigsten Argumente, die Sie hören, wenn Sie ein Lean-Projekt anregen?
Fröleke: Im Prinzip kann man die Argumente gegen Lean in fünf Blöcke einteilen: „Betrieb ist ungeeignet für den Lean-Ansatz“, „keine Zeit oder Kapazitäten“, „kein Geld für Investitionen“, „kein Platz“ und „Vorbehalte der Mitarbeiter“.
Das klingt nach viel Gegenwind.
Fröleke: Nach meiner Einschätzung haben 80 Prozent der produzierenden Unternehmen Vorbehalte gegen Lean Production, von der Geschäftsführung über die Produktions- und Fertigungsleiter bis hin zu den Mitarbeitern in der Produktion. Beginnen wir einmal mit der Geschäftsleitung. Eines der häufigsten Argumente kommt aus dem Bereich „Betrieb ungeeignet“, nämlich dass Geschäftsentwicklung und die Margen so gut sind, dass ein Lean-Projekt unnötig ist. Doch hohe Margen sollten nicht zu Untätigkeit führen, denn diese sind in der Regel endlich. Auch bei Nischenprodukten kann schnell Wettbewerb entstehen, und gerade dann sollte man hohe Margen nutzen, um schlanker und effizienter zu werden.
In eine ähnliche Richtung geht das Argument von Seiten der Produktionsleiter, dass der Lohnanteil am Produkt von +/- 9 % (Durchschnittswert in der deutschen Industrie) zu gering sei, um daran weiter zu sparen. In der Lean Production geht es aber nicht nur um die reine Fertigungszeit, dass gar die Mitarbeiter schneller und schneller gemacht werden sollen, sondern es geht in erster Linie um eine Verbesserung der Lager- und Materialorganisation. Oft sind den Verantwortlichen andere Kostenfaktoren wie der Materialeinkauf wichtig, die sie optimieren wollen. Tatsächlich sollte man jedoch Kosten, die unnötig sind, für eine saubere betriebswirtschaftliche Abrechnung reduzieren. Meine Erfahrung aus vielen Projekten ist, dass so Einsparungen zwischen 15 und 20 Prozent erreicht werden können. Dabei sind weiche Faktoren wie ergonomische Verbesserungen – die sich auch noch einmal positiv auf die Arbeitsleistung und Effizienz der Mitarbeiter auswirken – noch nicht berücksichtigt.
„Die Geschäfte laufen zu gut, als dass man etwas ändern müsste“, ist also ein Gegenargument. Warum glauben Betriebe außerdem, dass Lean bei ihnen nicht funktioniert?
Fröleke: Besonders oft hält man mir entgegen, dass die zu fertigenden Losgrößen zu klein seien, als dass eine Fließfertigung sich lohnen würde. Und damit verbunden, dass es zu häufige Variantenwechsel gäbe, die ein ständiges Umrüsten nötig machten. Da kann ich nur entgegnen: „Das sind ja ideale Voraussetzungen für die Einrichtung einer One-Piece-Flow-Fertigung“ – wenn man die Materialversorgung clever strukturiert und alle nötigen Betriebsmittel und Materialien direkt an der Fertigungslinie vorhält. Gründe für kleine Losgrößen sind z. B. dass der Markt nur geringen Bedarf hat oder dass starker Wettbewerb vorherrscht. Eine optimierte Fertigung unter Lean-Gesichtspunkten könnte der Schlüssel zu mehr Marktanteilen sein, da das Produkt in der Regel schneller und kostengünstiger angeboten werden kann. Was die Variantenwechsel angeht, kann ich die Umrüstzeiten durch eine One-Piece-Flow-Fertigung deutlich reduzieren und damit auch Lieferzeiten verkürzen – ebenfalls eine gute Voraussetzung, um Marktanteile zu gewinnen.
Lieferzeiten ist ein gutes Stichwort. Sie sagten mangelnde Zeit und mangelnde Kapazitäten seien ebenfalls ein Problem. Was hat es damit auf sich?
Fröleke: Viele Unternehmen sind stark in ihrem Alltagsgeschäft verhaftet und sehen keine Möglichkeit oder Kapazität, ein „zusätzliches“ Lean-Projekt zu realisieren. Dabei sind es genau die Lean-Bausteine, die helfen können, Zeit sinnvoller zu nutzen. Häufig höre ich von Produktionsleitern von einem hohen Auftragsbestand mit erheblichen Lieferproblemen. Das erfordert natürlich eine Analyse. Lieferschwierigkeiten werden vom Kunden nicht lange toleriert. Argumentiert wird dabei auch oft mit einem hohen Anteil an Fehlteilen, um die sich gekümmert werden muss, sodass keine Zeit für anderes bleibt. Doch diese führen wiederum zu Lieferschwierigkeiten und vielleicht einem Umsatzverlust. Gerade bei solchen internen Problemen ist ein Lean-Projekt für die Ursachenforschung geeignet. Wo liegen die Materialschwierigkeiten? Wo stockt es in der Produktion? Wie können Abläufe effizienter gestaltet, wie der Materialfluss verbessert und beschleunigt werden? Wenn man sich diese Analyse- und Planungszeit nimmt, ist auf mittlere Sicht eine deutliche Verbesserung der Produktions- und Lieferzeiten zu erwarten.
Es braucht also ein wenig Initialaufwand, um ein Lean-Projekt zu starten. Das bezieht sich ja nicht nur auf den Zeitfaktor, sondern auch auf die finanzielle Seite. Wie sind da die Reaktionen in den Unternehmen?
Fröleke: Oft sind es die Produktionsleiter oder die Leiter Industrial Engineering, die befürchten, für die benötigten Investitionen von der Geschäftsführung keine Genehmigung zu erhalten. Natürlich muss sich ein Projekt rechnen und dessen muss man sich sicher sein, bevor die Geschäftsführung einbezogen wird. Aber mit einer sinnvollen Wirtschaftlichkeitsrechnung, bei der wir von Treston auch beratend zur Seite stehen, lässt sich Überzeugungsarbeit leisten. Die kritische Schwelle sind in der Regel zwei Jahre. Wenn eine Umstrukturierung sich in weniger als zwei Jahren amortisiert, ist das der richtige Weg, um in den darauffolgenden Jahren einen guten Umsatz mit dem Produkt zu erzielen.
Wichtig ist, nicht zu viel auf einmal zu wollen. Man kann nicht versuchen, einen ganzen Bereich umzukrempeln, um dann zu merken, dass man sich übernommen hat. Das Projekt muss in seinem Umfang den Kapazitäten im Unternehmen angepasst sein. Es sollte anhand eines kleineren Pilotprojekts die Effizienz von Lean Production nachgewiesen werden. Dann kann gemeinsam mit der Geschäftsführung ein Projektplan erstellt werden, in dem einzelne Steps festgeschrieben sind, die nacheinander abgearbeitet werden. Damit ist sichergestellt, dass es nicht zu betrieblichen Störungen aufgrund des Lean-Projekts kommt.
Wenn man dann einmal erkannt hat, welches Potenzial in der Lean-Betrachtung steckt, ist es oft wie ein Sog, der sich Abteilung für Abteilung ausbreitet und wo dann ein Projekt nach dem nächsten umgesetzt wird. Das erste Projekt ist immer das aufwendigste und zeitintensivste, die folgenden lassen sich anhand der gemachten Erfahrungen viel effizienter umsetzen. Letztlich greift man dann bereits auf ein Datengerüst zurück: Genutzt werden können bestimmte Regale, Arbeitsstationen, Kästen für die Materialversorgung in bestimmten Maßen und Gewichten, und so erfolgt die Umsetzung in anderen Fertigungsbereichen viel schneller.
Bestimmt erfordert es auch ein gewisses Fingerspitzengefühl seitens der Verantwortlichen, eine solche Veränderung im Unternehmen durchzuführen und alle Beteiligten – von der Geschäftsführung bis zum Monteur – von dem Vorhaben zu überzeugen. Welche Erfahrungen haben Sie in Sachen innerbetriebliche Kommunikation gemacht?
Fröleke: Das ist eines der heikelsten Themen. So ein Lean-Projekt steht und fällt mit der Kommunikation im Unternehmen und der Einbeziehung aller beteiligten Mitarbeiter. Grundsätzlich bedeutet Veränderung erst einmal Gegenwind. Häufig höre ich von Produktions- oder Fertigungsleitern, dass eine Umstrukturierung zu viel Unruhe in den Betrieb und die Belegschaft bringe, dass Mitarbeiter aufgrund ihrer eigenen langjährigen Erfahrung zu viele Bedenken hätten und man die Dinge lieber belassen solle, wie sie sind.
Oft ist auch die Schnittstellenkommunikation zwischen den Abteilungen ein großes Problem. Da möchte das Lager nicht mit der Montage sprechen und niemand mit der Qualitätssicherung, die die Fehler der anderen bemängelt. Jeder erledigt seine Aufgaben auf die für ihn beste Weise, beachtet aber nicht den Gesamtproduktionszusammenhang. Darauf kommt es in der Lean-Betrachtung natürlich an. Abteilungsübergreifende Lean-Projekte sind hocheffizient, weil kostenintensive Schnittstellen, an denen die Verzögerungen entstehen, untersucht und beseitigt werden. Hand in Hand Arbeiten ist gefragt!
Wie gehen Sie es an, Bedenken der Mitarbeiter zu zerstreuen?
Fröleke: Leider wird in Unternehmen immer noch zu viel von oben nach unten verordnet. Ich appelliere an die Führungskräfte, solche Umstrukturierungsprojekte aktiv und zeitnah an die betroffenen Mitarbeiter in der Fertigung zu kommunizieren. Und dabei auch die Erfahrung der Mitarbeiter zu nutzen. Klar ist: Der Mitarbeiter entscheidet nicht, OB investiert wird, aber er kann daran teilhaben zu entscheiden, IN WAS investiert wird und wie die Abläufe sinnvoll verändert werden können. Wenn Mitarbeiter das Gefühl haben, dass auf ihre Belange aktiv eingegangen wird, ist die Bereitschaft, das Projekt zu unterstützen, viel höher. Ich plädiere für gemeinsame Workshops mit einem externen Moderator, in denen alle Beteiligten ihre Vorstellungen äußern können und man gemeinsam nach passenden Lösungen sucht.
Die Skepsis rührt oft auch daher, dass der Mitarbeiter denkt, er solle nur schneller und kostensparender für das Unternehmen arbeiten. Doch darum geht es bei Lean nicht. Mit dem Lean-Ansatz wollen wir den Stress für Mitarbeiter reduzieren, Abläufe erleichtern und die Tätigkeiten und Arbeitsplätze viel ergonomischer gestalten. Davon profitiert der Mitarbeiter, aber eben auch das Unternehmen dank höherer Motivation und geringerer Fehlzeiten. In vielen Fertigungsbereichen ist immer noch die Annahme weit verbreitet, wenn man den gleichen Handgriff 20 mal hintereinander durchführt, sei das die effizienteste Arbeitsweise. Tatsächlich schlagen sich zum einen solche einseitigen Belastungen gesundheitlich nieder, zum anderen bedeutet eine solche Produktionsweise eine unglaubliche Kapitalbindung. Wenn 20 Motoren in solch Einzelschritten nach und nach gefertigt werden, vergeht eine viel zu lange Zeitspanne, in der das Unternehmen mit dem Produkt noch kein Geld verdient. Fertigt das Unternehmen dagegen nach One-Piece-Flow kann der erste Motor nach kürzester Zeit verkauft und die erste Rechnung gestellt werden.
Zeit, Geld, Kommunikation, Eignung – da fehlt zu guter Letzt noch der Kritikpunkt „kein Platz“, den Sie eingangs in den Argumenten gegen Lean Production genannt hatten.
Fröleke: „Fehlender Platz in der Fertigung, um eine Umstrukturierung durchführen zu können“ ist tatsächlich ein etwas kurioser Aspekt. Der Produktionsleiter argumentiert dann, dass die Einzelarbeitsplätze nicht viel Platz beanspruchen würden, eine Fließfertigung dagegen auf der gleichen Fläche nicht zu realisieren sei. Das stimmt. Nur reicht es nicht aus, die reinen Arbeitsplätze zu betrachten, sondern es müssen alle benötigten Flächen zusammengefasst werden: die oft enormen Lagerflächen, die Material- und Arbeitsmittelbereitstellung, die Puffer. Ich kann Ihnen – ohne zu messen – sagen: Es wird immer funktionieren. Durch die Flächenreduktion in diesen sekundären Bereichen Lager und Materialbereitstellung ist die Fläche für eine lean-gerechte One-Piece-Flow-Linie stets realisierbar. In allen bisher von Treston umgesetzten Projekten.
Wie ich bei Ihrer ersten Frage schon erwähnt habe: Es gibt im produzierenden Bereich keine Gründe, die gegen die Einführung von Lean-Prinzipien sprechen. Es kommt nur darauf an, wie man das Projekt auf die Anforderungen vor Ort abstimmt. Dann kann ein Unternehmen davon nur profitieren.
Herr Fröleke, herzlichen Dank für das Gespräch!
Themen in diesem Fachartikel:
Unternehmensinformation / Kurzprofil:
Treston Deutschland GmbH aus Hamburg ist ein Tochterunternehmen der Treston Oy mit Hauptsitz in Finnland. Treston zählt zu den führenden europäischen Anbietern von industriellen Arbeitsplatzeinrichtungen sowie Lager- und Handhabungssystemen. Als einziges Unternehmen bietet Treston klassische Arbeitsplatzsysteme mit Arbeitstischen, Regalschränken, Arbeits- und Bürostühlen, Tischwagen und Beleuchtungen, Profiltechnik-Lösungen sowie Materialfluss-Systeme unter einem Dach. Auf eine gelungene Kombination von funktionaler Ergonomie und ansprechendem Design wird großen Wert gelegt. Neben der Treston Deutschland GmbH hat der Konzern weitere Tochtergesellschaften in Schweden, Frankreich, Großbritannien, Russland und den USA sowie Premium-Partner in Norwegen,
Treston Deutschland GmbH
Friedrich-Ebert-Damm 143
D-22047 Hamburg
Dirk Jonsson
Geschäftsführer
Tel.: 040 / 8816 5022-0
Fax: 040 / 8816 5022-10
E-Mail: dirk.jonsson(at)treston.com
Wassenberg Public Relations für
Industrie & Technologie GmbH
Rollnerstr. 43
D-90408 Nürnberg
Michaela Wassenberg
Tel.: 0911 / 598 398-0
Fax: 0911 / 598 398-18
m.wassenberg(at)wassenberg-pr.de
Datum: 07.03.2017 - 13:23 Uhr
Sprache: Deutsch
News-ID 1464418
Anzahl Zeichen: 0
Kontakt-Informationen:
Ansprechpartner: Dirk Jonsson
Stadt:
D-22047 Hamburg
Telefon: 040 / 8816 5022-0
Kategorie:
Industrietechnik
Anmerkungen:
Dieser Fachartikel wurde bisher 179 mal aufgerufen.
Der Fachartikel mit dem Titel:
"„Der Kern ist die Vermeidung von Verschwendung“
"
steht unter der journalistisch-redaktionellen Verantwortung von
Treston Deutschland GmbH (Nachricht senden)
Beachten Sie bitte die weiteren Informationen zum Haftungsauschluß (gemäß TMG - TeleMedianGesetz) und dem Datenschutz (gemäß der DSGVO).