Heinrich Georg Maschinenfabrik: Neue Bearbeitungszentren sparen 40 Prozent der Bearbeitungszeit
Komplettbearbeitung bis 250 Tonnen Werkstückgewicht mit drastisch reduzierten Nebenzeiten
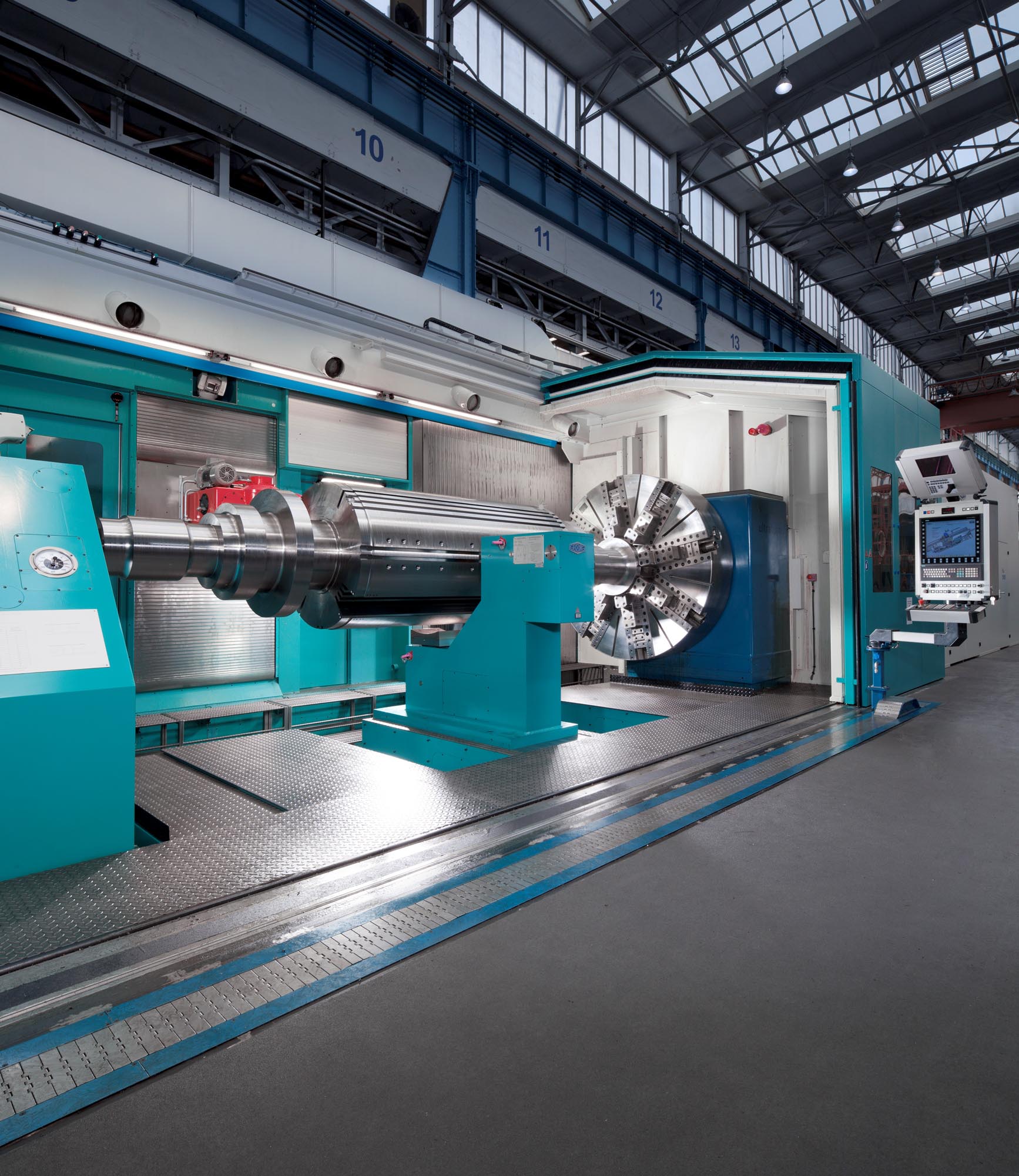
(IINews) - Auf der AMB präsentiert GEORG die Horizontal-Bearbeitungszentren der Serie ultraturn MC, die Werkstücke mit einem Gewicht bis zu 250 Tonnen Gewicht und 4.000 mm Durchmesser bearbeiten. Mit der erfolgreichen Inbetriebnahme der ersten Maschine bei der Siemens AG in Berlin sowie der Montage zweier weiterer Maschinen ist GEORG der weltweit einzige Hersteller von Bearbeitungszentren dieser Größenordnung, der das Konzept des Bearbeitens und Vermessens auf derselben Maschine realisiert.
Auf der diesjährigen AMB stellt GEORG die neuen Horizontal-Bearbeitungszentren der Serie ultraturn MC in der virtuellen Realität vor: Im "GEORG-Cinema" erleben die mit 3D-Brillen ausgestatteten Messebesucher die bis zu 30 m langen Maschinen zum Greifen nah.
GEORG hat die neuen Bearbeitungszentren für die Komplettbearbeitung von komplexen Werkstücken mit bis zu 250 t Gewicht und 4.000 mm Durchmesser entwickelt. Sie werden unter anderem für die Herstellung von Turbinen- und Generatorenläufern sowie für Kompressoren verwendet.
Vor Kurzem hat die Siemens AG für das neue Bearbeitungszentrum im Werk Berlin die Abnahme erteilt. Es ist das weltweit einzige für Werkstücke mit einem Gewicht von bis zu 180 t, in der das Bearbeiten und Vermessen in der gleichen Maschine realisiert ist. Es bearbeitet Werkstücke mit einem Durchmesser von bis 4.000 mm und einer Werkstücklänge bis zu 10.000 mm. Siemens besitzt weltweit bereits etwa 20 Maschinen von GEORG.
Die Erfahrungen aus dem Betrieb dieser Anlage der neuen Baureihe belegen, dass sich neben der deutlichen Steigerung der Präzision der Werkstücke eine drastische Zeitersparnis bei der Bearbeitung von rund 40 Prozent ergibt, unter anderem weil sie Nebenzeiten drastisch verkürzt. Eine Maschine der neuen Generation ersetzt in der Fertigung mehrere andere, die vorher nicht nur Personal für Fertigung und Wartung, sondern auch Platz und Kapital gebunden haben. Außerdem vereinfacht sie die Produktionsplanung deutlich, da nur noch ein Bearbeitungszentrum alle Arbeitsschritte ausführt.
Zwei weitere ultraturn MC Bearbeitungszentren hat GEORG bereits ausgeliefert, sie werden in Kürze in Betrieb gehen. Die Maschine, die GEORG zurzeit bei Doosan-Skoda in Pilsen/Tschechische Republik montiert, ist für ein Werkstückgewicht von bis zu 140 t bei einem Durchmesser von bis zu 3.500 mm und eine maximale Werkstücklänge von 12.000 mm ausgelegt.
Jan Ebener, der Vertriebsleiter Werkzeugmaschinen bei GEORG, erläutert, warum sein Kunde sich für die ultraturn MC entschieden hat: "Wir sind der weltweit einzige Anbieter, der für Werkstücke mit wahrhaft gigantischen Abmessungen neben der Fräs- auch die Dreh- und die Schleifbearbeitung auf der Maschine in einem schlüssigen Konzept kombiniert. Und wie bei dem Auftrag von Siemens konnten nur wir die Werkstückvermessung auf derselben Maschine realisieren."
Bei Iskra Turbogaz in Perm/Russland montiert GEORG zurzeit eine weitere ultraturn MC. Dort werden in Zukunft Werkstücke mit einem Gewicht von bis zu 25 t, einem Durchmesser bis 2.500 mm und einer Werkstücklänge von bis zu 7.000 mm gefertigt. Sie werden unter anderem für Kompressoren und Pumpen für die Öl und Gas fördernde Industrie benötigt. Bei der Innenbearbeitung dieser Bauteile punktet die Maschine mit Merkmalen wie der kombinierten Dreh- und Fräsbearbeitung sowie dem Bearbeiten von komplexen Konturen, die nicht parallel zur Mittelachse des Werkstückes verlaufen.
Alle drei Maschinen hat GEORG als an Kundenanforderung angepasste Komplettlösungen einschließlich der Peripheriesysteme geliefert.
Hintergrund: Messen ohne Umspannen
Bei der Bearbeitung von Werkstücken der genannten Größenordnung in unterschiedlichen Maschinen waren bisher für den Wechsel zwischen den Bearbeitungsschritten meist vier bis acht Stunden pro Maschine anzusetzen, was sich bei komplexen Werkstücken oft zu Wochen und Monaten summierte.
Neu ist, dass GEORG die Qualitätskontrolle jetzt in die Fertigung integriert. Die ultraturn MC ist das weltweit erste Bearbeitungszentrum, in dem für das Messen der Durchmesser nicht - wie bisher üblich - lediglich ein einzelner Taster verwendet wird. Das am Torständer angebrachte, mitfahrende Zwei-Punkt-Werkstückmesssystem arbeitet - wie eine große Mikrometerschraube - mit zwei Tastern und vermisst die Werkstücke direkt in der Maschine mit hoher Präzision.
Während das Messen von Durchmessern oder Planlauf bei Werkstücken von bis 2.000 mm mit Messmaschinen durchaus mehrere Stunden in Anspruch nehmen kann, benötigt das integrierte System lediglich wenige Minuten. Mit dieser Funktion ist Georg weltweit Vorreiter. Hinzu kommt, dass die Messung automatisch erfolgt und keine Mitarbeiter anderer Abteilungen zur Hilfe gerufen werden müssen.
Heinrich Georg auf der AMB 2016 in Stuttgart
13. bis 17. September 2016:
Halle 9 / Stand D51
Themen in diesem Fachartikel:
georg
werkst-ck
messmaschine
ultraturn
bearbeitungszentrum
amb
turbine
generator
kompressor
fr-sen
drehen
schleifbearbeitung
Unternehmensinformation / Kurzprofil:
www.georg.com
VIP-Kommunikation
Regina Reinhardt
Dennewartstraße 25-27
52068 Aachen
reinhardt(at)vip-kommunikation.de
+49.241.89468-24
www.vip-kommunikation.de
Datum: 10.08.2016 - 11:50 Uhr
Sprache: Deutsch
News-ID 1388129
Anzahl Zeichen: 0
Kontakt-Informationen:
Ansprechpartner: Jan Ebener
Stadt:
Kreuztal
Telefon: +49.2732779-306
Kategorie:
Forschung & Entwicklung
Anmerkungen:
Dieser Fachartikel wurde bisher 58 mal aufgerufen.
Der Fachartikel mit dem Titel:
"Heinrich Georg Maschinenfabrik: Neue Bearbeitungszentren sparen 40 Prozent der Bearbeitungszeit
"
steht unter der journalistisch-redaktionellen Verantwortung von
Heinrich Georg GmbH Maschinenfabrik (Nachricht senden)
Beachten Sie bitte die weiteren Informationen zum Haftungsauschluß (gemäß TMG - TeleMedianGesetz) und dem Datenschutz (gemäß der DSGVO).