Neuer Schmiedeprozess spart 20 Prozent Stahl
IPH entwickelt Querkeilwalzapparat in Flachbackenbauart für den industriellen Einsatz
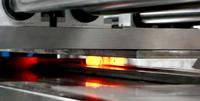
(PresseBox) - Common-Rails lassen sich künftig mit wesentlich weniger Materialeinsatz herstellen ? dank eines neuen Schmiedeprozesses, den das IPH gemeinsam mit Partnern aus ganz Europa entwickelt hat. Dabei wird das Bauteil mittels Querkeilwalzen vorgeformt und anschließend fertiggeschmiedet, sodass deutlich weniger Grat entsteht als bisher. Für kleine und mittelständische Unternehmen (KMU) hat das IPH einen besonders kompakten Querkeilwalzapparat in Flachbackenbauart konstruiert, der sich auch für kleine Stückzahlen rechnet. Es ist der erste Apparat dieser Art, der tatsächlich in der Industrie zum Einsatz kommt: Ein türkisches Schmiedeunternehmen will damit Vorformen für Hüftimplantate herstellen.
Ob Common-Rails für Einspritzanlagen oder Kurbelwellen im Motor: Geschmiedete Bauteile halten hohe Belastungen aus. Ihre Herstellung ist jedoch eine Belastung für die Umwelt, weil dabei deutlich mehr Material und Energie verbraucht wird, als eigentlich nötig wäre. Das Institut für Integrierte Produktion Hannover (IPH) erforscht und entwickelt deshalb seit Jahren ressourcenschonende Herstellungsprozesse.
Beim klassischen Gesenkschmieden wird ein Rohling aus Stahl auf rund 1200 Grad Celsius erwärmt und in eine zweigeteilte Form gelegt, das sogenannte Gesenk. Werden die beiden Gesenkhälften aufeinander gepresst, fließt das heiße Metall in die Form. Überschüssiges Material entweicht zu den Seiten und bildet den sogenannten Grat. Wenn das Bauteil abgekühlt ist, wird der Grat entfernt. Schmiedeunternehmen gehen damit sicher, dass die Form vollständig ausgefüllt wird und keine fehlerhaften Bauteile entstehen. Allerdings gehen auf diese Weise erhebliche Mengen an Material verloren, zumal oft mehrere Schmiedeschritte notwendig sind, um komplizierte Bauteile herzustellen.
Ein Common-Rail für Lastwagen beispielsweise benötigt bei der Herstellung 9,3 Kilogramm Edelstahl. Nach zwei Schmiedeschritten, bei denen jeweils Grat entsteht, wiegt das fertige Bauteil nur noch 6 Kilogramm. Bei der Herstellung von 1000 Common-Rails werden somit mehr als 3 Tonnen Edelstahl verschwendet.
Im Forschungsprojekt ?CoVaForm? hat das IPH deshalb ein neues Herstellungsverfahren entwickelt, das laut den Computersimulationen der Wissenschaftler rund 20 Prozent Material spart. Dabei wird das Bauteil mittels Querkeilwalzen vorgeformt: Das heiße Metall wird nicht in ein Gesenk gepresst, sondern zwischen zwei Keilen in Form gerollt. Beim Querkeilwalzen entsteht keinerlei Grat. Zwar ist weiterhin ein zweiter Schmiedeschritt nötig, bei dem Material verloren geht. Jedoch genügen für die Herstellung des Common-Rails nun 7,5 statt der ursprünglichen 9,3 Kilogramm Edelstahl ? das sind 20 Prozent weniger Material als zuvor. Außerdem spart der neue Herstellungsprozess Energie, weil eine kleinere Menge Stahl auf 1200 Grad Celsius erwärmt werden muss.
Trotz der hohen Einsparmöglichkeiten wird das Querkeilwalzen bisher kaum industriell eingesetzt, weil die Prozesse kompliziert und die Werkzeuge teuer sind. Bisherige Querkeilwalzapparate in Rundbackenbauart lohnen sich nur für sehr hohe Stückzahlen. Das IPH hat im Forschungsprojekt deshalb einen besonders kompakten Querkeilwalzapparat in Flachbackenbauart entwickelt, der nur ein Zehntel kostet ? und der sich somit auch für kleine und mittelständische Schmiedeunternehmen lohnt.
Mit der Maschine lassen sich nicht nur Vorformen für Common-Rails herstellen, sondern auch für Antriebswellen, Pleuel und viele weitere längliche Bauteile. Ein türkisches Schmiedeunternehmen will mit dem Querkeilwalzapparat des IPH künftig Hüftimplantate aus Titan schmieden. Die IPH-Ingenieure sind derzeit in der Türkei, um die Maschine einzurichten.
Gefördert wird das Forschungsprojekt ?CoVaForm? von der Europäischen Union. Neben dem IPH beteiligen sich zwei weitere Forschungsinstitute und vier Industrieunternehmen aus fünf Ländern, darunter ein Werkzeugbauer aus Spanien sowie das Schmiedeunternehmen aus der Türkei, das die Maschine künftig in der Produktion einsetzt. Der Projekttitel ?CoVaForm? steht für ?Conservation of valuable materials by a highly efficient forming system? ? also die Einsparung wertvoller Materialien durch hocheffiziente Umformtechnik. Ende Februar läuft das Projekt aus.
Weitere Informationen erhalten Sie unter www.covaform.eu.
Das Institut für Integrierte Produktion Hannover (IPH) gemeinnützige GmbH forscht und entwickelt auf dem Gebiet der Produktionstechnik. Gegründet wurde das Unternehmen 1988 aus der Leibniz Universität Hannover heraus. Das IPH bietet Forschung und Entwicklung, Beratung und Qualifizierung rund um die Themen Prozesstechnik, Produktionsautomatisierung, Logistik und XXL-Produkte. Zu seinen Kunden zählen Unternehmen aus den Branchen Werkzeug- und Formenbau, Maschinen- und Anlagenbau, Luft- und Raumfahrt und der Automobil-, Elektro- und Schmiedeindustrie.
Das Unternehmen hat seinen Sitz im Wissenschaftspark Marienwerder im Nordwesten von Hannover und beschäftigt aktuell 68 Mitarbeiter, 26 davon als wissenschaftliches Personal (Stand: Februar 2016).
Themen in diesem Fachartikel:
Unternehmensinformation / Kurzprofil:
Das Institut für Integrierte Produktion Hannover (IPH) gemeinnützige GmbH forscht und entwickelt auf dem Gebiet der Produktionstechnik. Gegründet wurde das Unternehmen 1988 aus der Leibniz Universität Hannover heraus. Das IPH bietet Forschung und Entwicklung, Beratung und Qualifizierung rund um die Themen Prozesstechnik, Produktionsautomatisierung, Logistik und XXL-Produkte. Zu seinen Kunden zählen Unternehmen aus den Branchen Werkzeug- und Formenbau, Maschinen- und Anlagenbau, Luft- und Raumfahrt und der Automobil-, Elektro- und Schmiedeindustrie.
Das Unternehmen hat seinen Sitz im Wissenschaftspark Marienwerder im Nordwesten von Hannover und beschäftigt aktuell 68 Mitarbeiter, 26 davon als wissenschaftliches Personal (Stand: Februar 2016).
Datum: 22.02.2016 - 16:07 Uhr
Sprache: Deutsch
News-ID 1324043
Anzahl Zeichen: 0
Kontakt-Informationen:
Ansprechpartner:
Stadt:
Hannover
Telefon:
Kategorie:
Maschinenbau
Anmerkungen:
Dieser Fachartikel wurde bisher 63 mal aufgerufen.
Der Fachartikel mit dem Titel:
"Neuer Schmiedeprozess spart 20 Prozent Stahl
"
steht unter der journalistisch-redaktionellen Verantwortung von
IPH - Institut für Integrierte Produktion Hannover gemeinnützige GmbH (Nachricht senden)
Beachten Sie bitte die weiteren Informationen zum Haftungsauschluß (gemäß TMG - TeleMedianGesetz) und dem Datenschutz (gemäß der DSGVO).