EPLAN und Sick: Maschinenkommunikation per OPC UA
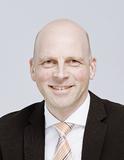
(PresseBox) - EPLAN und Sick präsentieren zur diesjährigen SPS IPC Drives neue Möglichkeiten der Maschinenkommunikation. Auf dem Gemeinschaftsstand ?Automation meets IT? zeigen beide Partner gemeinsam erste Industrie 4.0-Konzepte. Per OPC UA werden Einstellparameter während der Inbetriebnahme an eine Maschine übergeben. Das unterstützt eine schnellere Inbetriebnahme sowie neue Wartungsszenarien.
Die Flexibilität bei der Fertigung bis zur Losgröße 1 und Maschinenkommunikation inklusive der Übermittlung von Prozessdaten über das OPC UA-Protokoll stellen wichtige Lösungsansätze zur Umsetzung von Industrie 4.0 dar. Erste Beispiele zeigen EPLAN und Sensorhersteller Sick zur diesjährigen SPS IPC Drives auf dem Gemeinschaftsstand ?Automation meets IT? in Halle 3A. Im Wechselspiel zwischen der Hardwareplanung mit dem CAE-System und der Softwareplanung mit den Tools des jeweiligen SPS-Herstellers werden in der Engineering-Phase bereits Zuordnungen zu OPC UA-Variablen festgelegt. Dieses kann für Aktoren, Sensoren als auch für die I/Os der SPS erfolgen.
?Gemeinsam mit Sick nutzen wir die Erstvorführung auf der SPS IPC Drives, um mit potenziellen Anwendern zu diskutieren und die Praxis-Anforderungen kennenzulernen?, erklärt Thomas Michels, Leiter Produktmanagement bei EPLAN Software & Service. ?Weiteres Ziel ist es, die in der Inbetriebnahme, Produktion und Service gewonnenen Erkenntnisse bereits in der Engineering-Phase zu berücksichtigen.? Das EPLAN Data Portal bietet sich hierzu in Zukunft als tragende Säule zur Definition der in Industrie 4.0 notwendigen Gerätedaten der Automatisierungstechnik an.
Beispiel Sensortechnik
Klassisch nutzt der Hersteller einer Maschine oder Anlage die Software EPLAN zur Auslegung der Automatisierungstechnik. Das geschieht nicht nur in der Engineering-Phase innerhalb des eigenen PLM-Prozesses, sondern auch während der Inbetriebnahme beim Kunden. So lassen sich bereits im Engineering Einstellparameter beispielsweise für Sensoren im CAE-System vorbelegen. Während der Inbetriebnahme lassen sich diese Parameter aus der EPLAN Dokumentation per OPC UA an das Fertigungsmodul übertragen. Die einmal korrekt eingestellten Parametersätze einer Anlage sind im CAE-System und der Maschinen begleitenden Dokumentation erfasst und lassen sich somit in den Engineering-Prozess zurückführen. Die dadurch mögliche Mehrfachverwendung einmal erfolgreich eingestellter Subsysteme (?Klonen?) sowie die Weiterentwicklung von ?Documentation as built? zum ?Documentation as built and setup? stellen hierbei Mehrwerte für Inbetriebnehmer und Anlagenbetreiber dar.
Rüstzeiten reduziert
Unter Zuhilfenahme von OPC UA können zwischen der EPLAN Dokumentation und der Maschine nicht nur Parameterdatensätze, sondern bei Bedarf auch ausgewählte Prozessdaten übertragen werden. Diese können in Wartungsszenarien (Beispiel Fernwartung) und in der Re-Engineering-Phase genutzt werden, um Umbauten und Optimierungen gezielt vorzubereiten. Die neuen Einstellparameter werden dann in der Umbauphase direkt an die Anlage übertragen und reduzieren somit erneut die Rüstzeiten.
Die Vorteile im Überblick:
Lückenlose Dokumentation: Das Lesen von Einstellwerten aus den Sensoren in die EPLAN Dokumentation vervollständigt auf Knopfdruck die Maschinen und Anlagendokumentation um ausgewählte wichtige Bauteil-Parameter
Schnelle Inbetriebnahme: Das Schreiben der Einstellwerte aus der EPLAN Dokumentation an den Sensor erspart die manuelle Eingabe
Nutzen vervielfacht: Das Klonen der Einstellungen verkürzt die Engineering- und Inbetriebnahmezeiten
Bessere Fehleranalyse: Durch das Monitoring der Betriebszustände erhalten Unternehmen neue Möglichkeiten der Fehleranalyse
Prozessdaten analysieren: Anzeige und Auswertung der Prozessdaten und die Verknüpfung der Schaltplan-Logik im CAE erlauben zusätzliche Analysen in Maintenance und Re-Engineering
Kürzere Rüstzeiten: Neue Einstellwerte überschreiben führt zu reduzierter Rüstzeit bei Umbauten und Optimierungen
Daten gesichert: Rückführung der Erkenntnisse aus der Produktion ins Engineering (Voreinstellungen bei zentralen Gerätedaten z.B. im EPLAN Data Portal)
Service und Betrieb gestützt
Die neue Durchgängigkeit konsistenter Dokumentation bis hinein in Inbetriebnahme, Wartung und Betrieb ermöglicht besseren und vor allem schnelleren Service - beispielsweise bei der Verknüpfung von Schaltplan und Prozessdaten zur Optimierung des Re-Engineering oder auch in neuen Maintenance-Szenarien mit mobilen Endgeräten. Hier kann der Instandhalter online alle relevanten Steuerungsinformationen wie Schaltpläne und detaillierte Geräteinformationen nutzen. Die in EPLAN vorhandene Verschaltungslogik und die Geräteinformationen dienen dabei als wichtige Grundlage zur Datenanalyse und Vorhersage über Ausfallwahrscheinlichkeiten.
Sick AG
Sick ist einer der weltweit führenden Hersteller von Sensoren und Sensorlösungen für industrielle Anwendungen. Das 1946 von Dr.-Ing. e. h. Erwin Sick gegründete Unternehmen mit Stammsitz in Waldkirch im Breisgau nahe Freiburg zählt zu den Technologie- und Marktführern und ist mit mehr als 50 Tochtergesellschaften und Beteiligungen sowie zahlreichen Vertretungen rund um den Globus präsent. Im Geschäftsjahr 2014 beschäftigte Sick rund 7.000 Mitarbeiter weltweit und erzielte einen Konzernumsatz von 1.099,8 Mio. Euro.
Themen in diesem Fachartikel:
Unternehmensinformation / Kurzprofil:
Datum: 26.11.2015 - 08:17 Uhr
Sprache: Deutsch
News-ID 1291867
Anzahl Zeichen: 0
Kontakt-Informationen:
Ansprechpartner:
Stadt:
Monheim / Nürnberg
Telefon:
Kategorie:
Elektro- & Elektronik
Anmerkungen:
Dieser Fachartikel wurde bisher 83 mal aufgerufen.
Der Fachartikel mit dem Titel:
"EPLAN und Sick: Maschinenkommunikation per OPC UA
"
steht unter der journalistisch-redaktionellen Verantwortung von
EPLAN Software&Service GmbH&Co. KG (Nachricht senden)
Beachten Sie bitte die weiteren Informationen zum Haftungsauschluß (gemäß TMG - TeleMedianGesetz) und dem Datenschutz (gemäß der DSGVO).