Knappe Flächen besser nutzen: XXL-Montage soll produktiver werden
Forscher suchen Unternehmen, die ihre Baustellenfertigung optimieren wollen
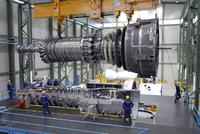
(PresseBox) - Sondermaschinen, Kräne oder Gasturbinen: Große Produkte ließen sich wesentlich produktiver fertigen, wenn die Hersteller den Platz in ihren Fabriken besser ausnutzen würden. Davon sind Wissenschaftler des Instituts für Integrierte Produktion Hannover (IPH) überzeugt. In einem Forschungsprojekt entwickeln sie derzeit einen Algorithmus, der die Baustellenfertigung optimieren soll. Für einen ersten Praxistest suchen sie noch Unternehmen, die ihre Produktivität steigern möchten.
Knappe Flächen besser nutzen: Von diesem Forschungsvorhaben profitieren vor allem Hersteller von XXL-Produkten. Denn während sich Alltagsprodukte wie Handys oder auch Autos äußerst effizient am Fließband fertigen lassen, ist die XXL-Fertigung noch verhältnismäßig unproduktiv. Die Produkte sind schlicht zu groß, um von Arbeitsstation zu Arbeitsstation bewegt zu werden, und werden deshalb in aller Regel in Baustellenfertigung hergestellt - das heißt, sie bleiben an einem festen Platz in der Fabrik.
Das Problem: Die Produktion beispielsweise von Sondermaschinen kann Monate dauern, und der Platzbedarf ändert sich mit der Zeit. Zum einen wächst das Produkt selbst mit jedem Montageschritt, zum anderen werden zwischenzeitlich immer wieder Flächen für Lager, Maschinen oder Gerüste benötigt. Trotzdem wird in den Fabriken meist eine feste Fläche für die Montage vorgesehen, auf der das fertige Produkt sowie sämtliche Nebenflächen Platz finden. Vollständig ausgelastet wird diese Fläche aber immer nur kurzzeitig, meist bleibt Platz ungenutzt.
Wissenschaftler am Institut für Integrierte Produktion Hannover (IPH) wollen das ändern. Ihr Ziel ist es, ein dynamisches Fabriklayout zu entwickeln, bei dem für jedes Produkt nur so viel Fläche blockiert wird, wie es im Augenblick benötigt. Ein Beispiel: Für die Produktion einer großen Maschine ist zu Beginn nur wenig Platz erforderlich, weil zunächst Vorarbeiten erledigt werden. Nach einigen Wochen werden die Einzelteile per Kran zusammengesetzt - der Platzbedarf ist maximal. Anschließend wird der Kran abgebaut und die letzten Kabel werden verlegt. Auf der freigewordenen Fläche könnten die Monteure dann schon mit den Vorarbeiten für das nächste Produkt beginnen - und wenn die fertige Maschine die Fabrik verlässt, ist wieder Platz für den Kran.
Die Forscher entwickeln derzeit einen genetischen Algorithmus, der das optimale Layout berechnen soll. Der Algorithmus erhält Informationen darüber, welches Produkt zu welchem Zeitpunkt wie viel Platz benötigt - und ermittelt dann, wo es in der Fabrik platziert werden muss und zu welchem Zeitpunkt die Produktion beginnen soll. Dabei werden auch Lagerflächen und Transportwege berücksichtigt. Gefördert wird das Projekt mit dem Titel "DynaFapXXL - Planung dynamischer Layouts in der Baustellenmontage von XXL-Produkten bei konkurrierenden Flächenbedarfen" von der Deutschen Forschungsgemeinschaft (DFG).
Für erste Praxistests suchen die Forscher noch Firmen, die große Produkte in Baustellenfertigung herstellen und die bereit sind, ihr Fabriklayout wissenschaftlich überprüfen zu lassen. "Mit unserem Algorithmus wollen wir ermitteln, welche Potentiale eine dynamische Flächennutzung mit sich bringt. Hierdurch können wir Unternehmen zeigen, welche Leistung sie maximal aus ihrer Fabrik holen können", sagt Michael Zenker, der das Projekt am IPH leitet. Davon profitieren beide Seiten: Die Wissenschaftler können ihre Methode validieren und die Unternehmen erfahren, ob und in welchem Ausmaß sie ihre Produktivität steigern können.
Interessierte Unternehmen melden sich bei Michael Zenker unter der Telefonnummer (0511) 279 76-444 oder per E-Mail an zenker(at)iph-hannover.de.
Das Institut für Integrierte Produktion Hannover (IPH) gemeinnützige GmbH ist ein Dienstleister auf dem Gebiet der Produktionstechnik und wurde 1988 aus der Leibniz Universität Hannover heraus gegründet. Das IPH bietet Forschung und Entwicklung, Beratung und Qualifizierung rund um die Themen Prozesstechnik, Produktionsautomatisierung, Logistik und XXL-Produkte. Zu seinen Kunden zählen Unternehmen aus den Branchen Werkzeug- und Formenbau, Maschinen- und Anlagenbau, Luft- und Raumfahrt und der Automobil-, Elektro- und Schmiedeindustrie.
Das Unternehmen hat seinen Sitz im Wissenschaftspark Marienwerder im Nordwesten von Hannover und beschäftigt aktuell 61 Mitarbeiter, 29 davon als wissenschaftliches Personal (Stand: 1. Januar 2015).
Themen in diesem Fachartikel:
Unternehmensinformation / Kurzprofil:
Das Institut für Integrierte Produktion Hannover (IPH) gemeinnützige GmbH ist ein Dienstleister auf dem Gebiet der Produktionstechnik und wurde 1988 aus der Leibniz Universität Hannover heraus gegründet. Das IPH bietet Forschung und Entwicklung, Beratung und Qualifizierung rund um die Themen Prozesstechnik, Produktionsautomatisierung, Logistik und XXL-Produkte. Zu seinen Kunden zählen Unternehmen aus den Branchen Werkzeug- und Formenbau, Maschinen- und Anlagenbau, Luft- und Raumfahrt und der Automobil-, Elektro- und Schmiedeindustrie.
Das Unternehmen hat seinen Sitz im Wissenschaftspark Marienwerder im Nordwesten von Hannover und beschäftigt aktuell 61 Mitarbeiter, 29 davon als wissenschaftliches Personal (Stand: 1. Januar 2015).
Datum: 17.06.2015 - 11:40 Uhr
Sprache: Deutsch
News-ID 1226283
Anzahl Zeichen: 0
Kontakt-Informationen:
Ansprechpartner:
Stadt:
Hannover
Telefon:
Kategorie:
Forschung & Entwicklung
Anmerkungen:
Dieser Fachartikel wurde bisher 95 mal aufgerufen.
Der Fachartikel mit dem Titel:
"Knappe Flächen besser nutzen: XXL-Montage soll produktiver werden"
steht unter der journalistisch-redaktionellen Verantwortung von
IPH - Institut für Integrierte Produktion Hannover gemeinnützige GmbH (Nachricht senden)
Beachten Sie bitte die weiteren Informationen zum Haftungsauschluß (gemäß TMG - TeleMedianGesetz) und dem Datenschutz (gemäß der DSGVO).