Versagensgründe für Elektroisolationen
Die Durchschlagspannung in Datenblättern gibt dem Ingenieur an, bei welcher Spannung ein Isolationsmaterial versagt. Stillschweigend wird dabei die Kenntnis vorausgesetzt, dass dieser Wert nur im ?Neuzustand? Gültigkeit besitzt.
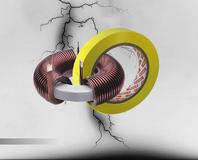
(PresseBox) - --> Der vollständige Artikel mit Grafiken ist hier im PDF-Format erhältlich <--
Für die Prüfung dieses Durchschlagens durch den Isolationswerkstoff hindurch wird meistens ein Spannungsanstieg von 500V/Sek verwendet. Die Durchschlagsspannung wird dann normiert auf die Dicke als z.B. kV/mm angegeben.
Doch dieser Wert verringert sich im Laufe der Einsatzzeit immer mehr. Eine Vielzahl von Faktoren ist daran beteiligt, die Isolationsfähigkeit eines Werkstoffes negativ zu beeinflussen. Darum reicht es je nach Anwendung auch nicht, den einzelnen Einflussfaktor zu betrachten. Vielmehr muß man die Summe aller Belastungen im konkreten Fall zusammengefasst in ihren Auswirkungen berücksichtigen.
Im Folgenden soll versucht werden, anhand der am häufigsten vorkommenden Belastungsarten einen Eindruck zu gewinnen, worauf man achten sollte:
1. Temperatur
Ganz allgemein kann festgestellt werden: je höher die Temperatur, desto stärker werden u.a. korrosive und oxidative Einflüsse der Umgebungsluft wirksam. Oder noch allgemeiner gesagt erhöht sich mit steigender Temperatur die Geschwindigkeit der Alterung, wobei die meisten Prozesse der sogenannten Arrhenius-Kurve gehorchen.
Als Faustregel aus der Elektronik rechnet man vereinfacht mit einer Halbierung der Lebensdauer je 10°C Temperaturerhöhung.
Isolationsmaterialien werden durch die IEC 60085 (Elektrische Isolierung, thermische Bewertung und Bezeichnung) in Wärmeklassen (z.B. B=130°C, F=155°C, H=180°C) eingeteilt. Diese Klassen geben an, bei welcher Dauergebrauchstemperatur die Isolationsmateria-len nach 20.000 Stunden noch 50% der Durchschlag-spannung haben, die sie im Neuzustand hatten.
Etwas anders formuliert bedeutet dies, dass ein Material nach nicht einmal zweieinhalb Jahren Einsatz bei maximaler erlaubter Temperatur die Hälfte seiner Schutzfunktion gegen einen elektrischen Schlag eingebüßt hat. Und dies alleine durch die thermische Alterung.
Will man also bei einer gegebenen Arbeitstemperatur eine höhere Lebensdauer erzielen, setzt man ein Isola-tionsmaterial einer höheren Wärmeklasse ein. Das übliche End-of-life-Kriterium der ?halbierten Durchschlagsspannung? wird auf diese Weise viel später erreicht.
Bezüglich der maximal auftretenden Wärme sollte man u.a. auch Wärmestaus innerhalb von Wicklungen, Stromdichteanstieg an Ausleitungen, höchste mögliche Umgebungstemperatur sowie ggf. gelegentlich auftretende Fehlfunktionen mit in die Betrachtung aufnehmen.
Werkstoffe wie Formmassen (z.B. Spulenträger), Lacke, Tränkmittel und Vergussmassen, die als Isolation eingesetzt werden, können durch Wärme verspröden, schrumpfen oder Spannungsrisse bekommen. Bei Flächenisolationsmaterial (z.B. NMN, DMD, usw.) kann es zu Delaminationen kommen, an denen durch den Epsilon-r-Sprung ähnlich wie bei Lunkern in Vergußmassen Tei-lentladungen entstehen können. Zusätzlich lässt Bewitterung zusammen mit Wärme diese Werkstoffe früher versagen.
2. Spannung (Stress, Teilentladung)
Bereits ab 400V entsteht Corona-Entladung an Oberflä-chen. Dabei werden durch die entstehende Feldstärke freie Elektronen soweit beschleunigt, dass sie weitere Ladungsträger aus ihrer stabilen Position schleudern. Es entwickelt sich eine Ladungsträgerlawine, die dann in eine Teilentladung (Corona- bzw. Gleitentladung) mündet.
In Gerätestromkreisen moderner Geräte wie Netzgeräten, Filterkomponenten und Powermodul-Antrieben kommt es vermehrt zu sich wiederholenden, energiereichen Impulsen (Schaltimpulse). Sie haben kurze Anstiegszeiten und Scheitelspannungen deutlich über dem Nennwert der Versorgungsspannung.
Diese Impulse lassen Isolationssysteme auf andere Weise altern wie unter herkömmlicher, netzfrequenter Wechselspannung:
-Teilentladungen zerstören die Isolation durch aggressive Abbauprodukte, UV-Strahlung und Ozon
-Ausbildung von Leitpfaden auf der Oberfläche der Isolation
-Elektromechanische Ermüdung auf Grund der Stromimpulse
-Dielektrische Erwärmung wegen der hochfre-quenten Anteile der Spannungsimpulse
Selbst wenn die Nennspannung unterhalb der TE-Einsetzspannung liegt, können solche überlagerten Impulse Teilentladungen zünden. Dabei beeinflussen die Temperatur, die Luftfeuchtigkeit, die Impulsform, -polarität und ?wiederholungsrate wesentlich die Degrationsgeschwindigkeit der Werkstoffe.
Ein ausreichender Abstand zur TE-Verlöschungsspannung ist also immer ratsam. Diese erreicht man ? neben konstruktiven Maßnahmen - durch Verwendung ausreichend spannungsfester, sprich ?dicker? Isolationen.
Das widerspricht allerdings den Anforderungen nach möglichst wenig Isolationsmaterial innerhalb von Trans-formatoren und Generatoren. Denn nur die ?Eisen-? und Kupferanteile in einem Transformator sind elektrisch wirksam. Außerdem ändert sich die Situation der kapa-zitiven und induktiven Kopplung deutlich.
Kann man die Gefahr von Teilentladungen nicht ausschließen, verwendet man Materialien, die besonders TE-beständig sind. Dazu gehören alle anorganischen Isolationsstoffe wie Glas, Keramik oder der Naturstoff Glimmer (Mica). Sie werden von Corona Entladungen nicht geschädigt. Eine erhöhte Corona Beständigkeit bei Flächenisolierstoffen, wie z.B. NOMEX-Aramid-papier T 418, wird durch die Einbringung von Feinglim-merplättchen erreicht. Dadurch wird die Corona-Beständigkeit von Hochspannungsmaschinen (Generatoren, Motoren) merklich verbessert werden. Dies gilt natürlich auch für den Isolationsaufbau von Motoren, die an Frequenzumrichtern (Invertern) betrieben werden.
In großen Anlagen (Motoren, Generatoren, Verteiltrans-formatoren) kann man halbleitende Materialien einset-zen, um diese Gleit- und Glimmentladung so weit wie möglich zu vermeiden. Auf diese Weise wird das elekt-rische Feld soweit geformt, dass keine Feldlinienkon-zentrationen entstehen können.
Diese Konzentration von Feldlinien an Kanten und Spitzen belastet deutlich stärker Isolationsmaterialien wie ein homogenes, flächiges E-Feld (z.B. die Kanten iso-lierter Kupferbänder).
Bei kleineren Baugrößen und wo man TE-Entladungen nicht ganz vermeiden kann empfiehlt sich der Einsatz von Kapton® CR oder Fluorpolymere wie z.B. FEP. Bei Kapton® CR wird die TE-Beständigkeit durch die Zuga-be von anorganischen Werkstoffen in die Polymermasse drastisch erhöht. Fluorpolymere bestechen durch ih-re geringe Reaktivität und niedriges Epsilon-r, haben jedoch andere Nachteile (Dehnbarkeit, Kaltfluß).
Vergussmassen sind ein gängiges Mittel, um Oberflächenentladungen (Corona) zu vermeiden. Durch die all-seitige Umhüllung mit in der Regel Polyurethan oder Epoxidharz vermindert man Epsilon-r-Sprünge und verhindert Entladungen durch die Luft. Von Haus aus bringen sol-che Vergussmassen keine besondere Teilentladungsfestigkeit mit, erlauben jedoch einen beliebig hohen Schichtaufbau, um einen hohe nominelle Durchschlagsfestigkeit zu erzielen. Entscheidend beim Einsatz von Vergussmassen in Hochspannungsanwendungen ist allerdings die Blasen- und Lunkerfreiheit, die man durch das an den Einzelfall angepassten Vakuumvergussverfahren (ggf. mit anschließender Druckbeaufschlagung zur Verbesserung der Durchimprägnierung) erzielt.
Wie bei den Betrachtungen zu dem Einfluss der Temperatur gilt auch hier, dass der Einsatz einer höherwertigen Materials (also z.B. statt Class B eine Class F Ma-terial, Kapton® CR statt Kapton® HN oder 50µm statt 25µm Folienstärke) den Zeitpunkt der Zerstörung deut-lich verschiebt. Die Spannungsfestigkeit bleibt im Dauerbetrieb länger oberhalb der Spannung, bei der Teilentladungen einsetzen.
Die IEC 60343 (Empfohlene Prüfverfahren zur Bestimmung der relativen Beständigkeit isolierender Werkstoffe gegen Durchschlag infolge Oberflächenteilentladung; ähnlich aber nicht gleich ASTM 2275) beschreibt ein beschleunigtes Verfahren, aus der sich dann die Zeit bis zum Ausfall bei geringerer Spannungsbelastung extrapolieren lässt. Eine weitere wichtige Norm zu dem Thema ist die DIN IEC/TS 61934 (Elektrische Messung von Teilentladungen (TE) bei sich wiederholenden Spannungsimpulsen mit kurzer Anstiegszeit).
Fazit: Die Vermeidung von Teilentladungen im Isolationssystem bleibt jedoch trotz verbesserter Isolationsmaterialien oberstes Gebot bei der Auslegung von elektrischen Betriebsmitteln. Das bei solchen Coronaentladungen entstehende UV-Licht, die aggressiven Abbauprodukte sowie das reaktive Ozon beeinträchti-gen ganz allgemein die umgebenden Materialien und nicht nur das direkt betroffene Isolationsmaterial.
Anmerkung1: die Messung der Höhe von TE in einem elektrischen Bauteil ist heute gängige Methode der Fer-tigungsüberwachung.
Anmerkung2: Positive bzw. negative Gleichspannung belastet Isolationsmaterialien auf unterschiedliche Weise. Es entstehen keine Verluste durch das Wechselfeld. Allerdings können dennoch Teilentladungen entstehen. Außerdem kann es zu einer Materialwanderung kom-men.
Anmerkung3: Eine umfassende Betrachtung des Alte-rungsverhaltens komplexer Isoliersysteme bietet die Norm IEC 60505 (Bewertung und Kennzeichnung von elektrischen Isoliersystemen)
3. Frequenz
In sehr vielen ?elektrischen? Basisnormen wird normalerweise mit sinusförmiger Spannung bei 50/60Hz ge-messen (IEC 60243, Elektrische Durchschlagfestigkeit von isolierenden Werkstoffen - Prüfverfahren). Moderne Schaltnetzteile arbeiten jedoch mit bedeutend höheren Frequenzen. Dadurch steigt der Stress für das Isolationsmaterial.
Exkurs: Die elektrische Größe ?Spannung? macht eine Aussage über die Kraft, die notwendig ist, um eine La-dungseinheit zu bewegen. Diese ?Arbeit? wird bei steigender Wechsel-Frequenz immer häufiger in das Isolationsmaterialien eingebracht. Unpolare Werkstoffe wie Keramiken oder Glas sind davon wenig betroffen. Die organischen Isolationsmaterialien wie PE, PA, EP, PUR, PP, PET, PA, PI usw. sind jedoch mehr oder we-niger polar.
Die komplexen Polymerketten bilden Dipole, die sich nach dem äußeren elektrischen Feld auszurichten versuchen. Es entsteht ein mechanischer Stress und mate-rialintern ?Reibungswärme?. Die Folge ist eine verringerte Spannungsfestigkeit.
Umpolarisierungsverluste in Isolationswerkstoffen (Quelle:CMC)
Bei dem Hochfrequenzschweißen macht man sich diese Umpolungsverluste im Material sogar zunutze, um den Kunststoff aufzuschmelzen (dipolartige Kunststoffe wie PVC, PA und Acetate; hohe dielektrische Verluste). Ganz grob kann man sagen: je höher das angelegte elektrische Feld und je höher die Frequenz, umso mehr Wärmeenergie wird in das Material eingetragen.
Was beim Schweißen erwünscht ist, ist für ein Isolati-onsmaterial im Dauereinsatz schädlich. Denn diese ?innere? Erwärmung bleibt häufig unbeachtet bei Alte-rungsbetrachtungen und wird über übliche Norm-Messungen (z.B. UL 746) nicht abgebildet.
MaterialDielektr. Verlustfaktor; (x10e-4)
50 Hz1 MHz
PTFE0,50,7
PP2,53,5
PI311
PET20210
PVC120300
PA (luftfeucht)39001300
Übersicht einiger Isolationsstoffe und ihrer Verluste im elektrischen Wechselfeld bezog auf zwei verschiedene Arbeitsfrequenzen
Frequenzumrichter und Schaltnetzteile belasten heute Isolationen mehr als früher, denn Motoransteuerungen oder z.B. Computernetzteile verwenden pulsweitenge-steuerte Spannungen im Bereich von 20 kHz und mehr.
Die dabei entstehenden Oberwellen haben Frequenzen bis weit über 50 MHz und es entstehen z.B. durch Re-sonanzen und induktive oder kapazitive Kopplung Spit-zenspannungen weit oberhalb der Betriebsspannung.
Die hohen Schaltgeschwindigkeiten dv/dt belasten er-heblich die verwendeten Isolationsmaterialien (P= U² ? C tan ?(T) ? Verlustleistung im Material). Zu-sätzlich können Wellenreflektion, Stehwellen und Rückwirkungen aus dem gespeisten Gerät weiteren Stress für die Isolation bewirken. Ausserdem erhöht sich die Belastung durch die kapazitive Kopplung z.B. von Phase zu Erde oder Phase zu Phase.
Das folgende Diagramm stellt diesen Zusammenhang für die häufig verwendete Polyesterfolie dar:
Die Angabe der Durchschlagspannung für Elektroisolierstoffe erfolgt in vielen Datenblättern bezogen auf ei-ne Arbeitsfrequenz von 50/60 Hz sinusförmigen Stroms (IEC 60243, Elektrische Durchschlagfestigkeit von isolierenden Werkstoffen). Wie im Diagramm dargestellt, reagieren jedoch viele der Standardisolationsfolien bei höheren Frequenzen mit einer deutlich verringerten Durchbruchspannungsfestigkeit.
Wichtiger Hinweis: Die normierte Durchschlagspannung wächst bei zunehmender Materialstärke nicht proporti-onal mit. Vielmehr wird durch die Verluste innerhalb des Materials die Durchbruchspannung in V/µm bei größerer Stärke signifikant geringer.
Durchschlagspannung versus Materialstärke bei Polyesterfolie (Quelle: CMC)
Fazit: Neben der Alterung durch Temperatur und die Schwächung des Materials durch Teilentladungen be-stimmt also auch die Frequenz maßgeblich die Überlegungen zur Auslegung eines elektrischen Gerätes.
4. Verhalten bei Verschmutzung (Umwelt)
Werden Oberflächen von Isolierstoffen durch Feuchtigkeit und Staub verunreinigt, entstehen bei einsetzenden Gleitentladungen langsam aber sicher Leitpfade. Diese bestehen aus karbonisierten Überresten der Verschmutzung und dem zerstörten Isolationsstoff. Diese Leitpfade breiten sich meist in Verästelungen (treeing) immer weiter aus und können am Ende zum Versagen der Isolation führen. Innerhalb von Vergüssen oder Formteilen kommt es zu ähnlichen Erscheinungen, besonders wenn diese versprödet und rissig sind.
Ein wesentlicher Aspekt dabei ist die mögliche Was-seraufnahme des Isolierstoffes, denn dadurch wird die Zerstörung auch innerhalb des Werkstoffes beschleu-nigt. Bestimmte Produkte, die mittels Polykondensation (z.B. Polyesterfolien) hergestellt werden, können bei Anwesenheit von Feuchtigkeit und Temperaturen ab 80°C sogar relativ schnell durch Hydrolyse geschädigt werden.
Um angeben zu können, wie leicht ein Werkstoff dazu neigt, auf der Oberfläche leitfähige Pfade auszubilden, verwendet man den sogenannten CTI-Wert bzw. die Kriechstromfestigkeit. Der Comparative Tracking Index gemäß DIN EN 60112 (Verfahren zur Bestimmung der Prüfzahl und der Vergleichszahl der Kriechwegbildung von festen, isolierenden Werkstoffen; ebenso UL 746 B) wird wie folgt gemessen: Zwei Elektroden werden auf die zu messende Oberfläche aufgelegt. Dazwischen wird eine leitfähige Salzlösung getropft und eine Spannung angelegt. Diejenige Spannung, bei der durch Überschläge die Oberfläche des Werkstoffes abgetra-gen wird, klassifiziert ihn dann in eine von 6 Stufen.
Diese besondere Kombination aus Gleitentladung und verschmutzter Oberfläche führt noch schneller wie tro-ckene Teilentladungen zur Zerstörung des Isolationswerkstoffes. Besonders bei elektrischen Einrichtungen, die im Außenbereich mit der Möglichkeit zur Betauung eingesetzt werden, sind deswegen erhöhte Abstände vorgeschrieben (siehe u.a. EN 61558, Sicherheit von Transformatoren, Netzgeräten, Drosseln und dergleichen).
MaterialCTI-Wert
(0 = hervorragend)
PUR Vergussmassen1...2
PEN 1
PET 1
PA 1
PE 1
PTFE 1
FR4 EP-Glasfaser3
PI 4
PEEK 4
5. Konstruktive Maßnahmen
Es gibt mehrere Möglichkeiten, um die elektrische Si-cherheit auch nach Tausenden von Betriebsstunden si-cherzustellen.
Die Erhöhung von Luft- und Kriechstrecken trägt als wesentlicher Schutz dazu bei, das auch bei gealtertem Isolationsmaterialien durch die dann verringerte Spannungsfestigkeit nichts passiert. Die erforderliche Luft- und Kriechstrecke ist insgesamt eine Funktion von cti, Verschmutzungsgrad, Überspannungskategorie, Frequenz und Einsatzgebiet (Haushalt, Industrie, Medizin).
Zusätzlich kann man zum Beispiel die Konstruktion feh-lertoleranter gestalten. Relativ einfach und dennoch hochwirksam ist oft der Einsatz eines Isolationsstoffes der nächsthöheren Isolations- bzw. CTI-Klasse. Die Zeit bis zum Versagen kann so normalerweise um mindes-tens das Doppelte erhöht werden.
Außerdem ist die Qualität der verwendeten Materialien mitbestimmend für die Leistungsfähigkeit über die gesamte Betriebszeit. So ist zum Beispiel die Wärmestandfestigkeit einer Polyimid-Folie deutlich abhängig vom Herstellverfahren. Die gleiche chemische Bezeichnung bedeutet nicht automatisch gleiche Eigenschaften. Die Klassifizierung der Wärmeklasse, bis zu der das Material eingesetzt werden darf, ist dagegen ein guter Anhaltspunkt.
Schlussendlich sind natürlich auch die mechanischen Belastungen bei der Verarbeitung (z.B. Zugbelastung auf Lackdraht) und die mögliche Vorschädigung durch Testverfahren zur Fertigungsüberprüfung (z.B. Hoch-spannungstest) mit lebensdauerbestimmend.
6. Weitere mögliche Ursachen
Temperatur, Spannungsstress, ungünstige Materialeigenschaften und Teilentladungen sind gewiss die am stärksten wirkenden Abbau-Mechanismen für Polymere. Es gibt jedoch weitere Faktoren, die je nach Einsatzort eine Rolle spielen können.
Nahezu alle Kunststoffe werden durch Strahlung (UV-Licht, Radioaktivität) geschädigt. Die energiereiche Strahlung zerstört die Polymerketten und führt z.B. zu einer geringeren mechanischen Festigkeit.
Etwas Ähnliches kann bei speziellen Kunststoffen wie Polyester, Polyamid und Polyimid durch die sogenannte Hydrolyse passieren. Dabei werden bei ausreichend hoher Energie (z.B. Wasserdampf bei 90°C) die Bindungen der Polymerkette durch den Dipol H2O aufgespalten. Tests an 50µm starker Polyesterfolie haben gezeigt, dass bereits nach 1.500 Stunden bei 85°C/85%relH die mechanische Festigkeit weitgehend verloren geht. Die Folie bricht bei einem Knickversuch (DIN EN 61234, Prüfverfahren für die Hydrolysebestän-digkeit von Elektroisolierstoffen)
Der sogenannte ?Motoretten-Test? (z.B. UL 1446) be-rücksichtigt bei der Beurteilung von Isolierstoffen auch deren Beständigkeit gegenüber mechanischer Vibration, wie sie in drehenden Maschinen vorkommen. Damit wird geprüft, ob der Kunststoff unter Reibeinwirkung zur Erosion neigt und damit verringerter Spannungsfestigkeit.
Ein ständiger Temperaturwechsel (z.B. nur zeitweiser Betrieb) belastet besonders Verbünde aus Isolations-material und Kernmaterial bzw. Lackdrähte. Die Aus-dehnungskoeffizienten von Kunststoffen liegen üblicherweise weit über denen von Metallen. Dies kann vor allem in vergossenen Systemen zu Spannungsrissen führen.
MaterialAusdehnungskoeffizient
in (*10-6 *K-1)
Aluminium23,1
Eisen11,8
Kupfer16,5
PET ? Polyester~80
PA ? Polyamid~120
PI ? Polyimid~56
PE - Polyethylen~200
Schlussendlich spielt auch die chemische Kompatibilität aller verwendeten Materialien in einem Isoliersystem (UL 1446, IEC 61858 und IEC 61857) eine Rolle bei der Alterungsbeständigkeit der einzelnen Komponenten. In Langzeit-Alterungstests oder verkürzten Prüfungen (Sealed Tube Test) wird das Zusammenspiel aller Isolationswerkstoffe bei Alterung geprüft. Inkompatibilitäten zeigen sich durch eine reduzierte Spannungsfestigkeit.
7. Zusammenfassung:
Heutige Geräte werden unter der Maxime ?kleiner, schneller, leistungsfähiger? konstruiert. Entwickler versuchen durch möglichst kleine Isolationsabstände (bei erschwerter Entwärmung) und durch deutlich höhere Frequenzen diesen Anforderungen gerecht zu werden.
Die Ökodesign-Richtlinie 2009/125/EG (E-Motoren auch 2009/640/EG) zwingt zudem spätestens seit Ende 2011 Hersteller zu energieeffizienterem Design, was meist gleichbedeutend ist mit einer höheren Energiedichte und den daraus resultierenden Folgen.
Die Datenblattangaben von Isolierstoffen spiegeln den optimalen Wert der Isolationsfähigkeit unter standardi-sierten Bedingungen am Anfang der Einsatzzeit wieder.
Während des Betriebs beeinflusst Temperatur die Isolationsfolien durch beschleunigte Alterung / Versprödung und damit einhergehend verringerter Spannungsfestigkeit.
Hohe Spannung schädigt das Material z.B. durch Gleit-entladungen und elektrischen Stress.
Bei höheren Frequenzen bricht die Spannungsfestigkeit besonders bei polaren Materialen stark ein.
Verschmutzungen und Feuchtigkeit können zur Ausbildung leitfähiger Pfade an der Oberfläche führen.
Chemische Belastungen, Hydrolyse und mechanischer Druck während der Herstellung setzen dem Isolationsmaterial weiter zu.
Für die sichere Auslegung eines elektrischen Gerätes ist es also notwendig, alle auftretenden Einflussgrößen in ihrer Wirkung aufzusummieren. Bei diesen Überle-gungen lohnt es sich, die erforderliche Spannungsfestigkeit am Ende der erwarteten Lebensdauer zu kennen. Denn sie bestimmt wesentlich mit, welche Materialien mit welchen Anfangseigenschaften eingesetzt werden sollten.
Da aber die Summe der Einflussgrößen am konkreten elektrischen Bauteil meist weder rechnerisch noch durch Tests ermittelbar ist, helfen Bauteilnormen wie die IEC 61558, Materialnormen wie die UL 510 oder IEC 60674 und Normen zur Messung wie die IEC 61934, IEC 60343, IEC 60034-27 oder UL746 dabei, geeignete und praxiserprobte Lösungen zu finden.
8. Ergänzende Informationen Isoliersysteme
Ein Möglichkeit zum Aufbau von Geräte-Isolationen ist die Verwendung von Elektroisoliersystemen (EIS). Diese Materialsammlungen werden nach standardisierten Verfahren (UL1446, IEC 61858, IEC 61587) zusammen mit Lackdraht geprüft. Sie bieten gegenüber ?wilden Materialkombinationen? eine erhöhte Sicherheit in Bezug auf die chemische Kompatibilität und das Alterungsverhalten.
Unterschieden wird zwischen ?Erprobten Elektroisoliersystemen?, für die Felderfahrungen vorhanden sind und noch unbekannte Isoliersysteme. Erprobte Isoliersysteme können durch einem Component Compatibility Test (CCT; Seald Tube Test) mit neuen Materialien (z.B. Klebebänder, Isolier-schläuche, Lagenisolationen) ergänzt werden.
Dem gegenüber wird bei vollständig neuen EIS ein Langzeit-Alterungstest (FTA, Full Thermal Aging Test) verwendet, der neben der Wärmebelastung auch Wärmezyklen und Feuchtigkeitsbelastung beinhaltet.
Zu diesem Thema existiert ein weiteres Informations-blatt, in dem detailliert die Vorgehensweise beschrieben wird.
Übersicht der zitierten Normen:
IEC 60085 Elektrische Isolierung, thermische Bewertung und Bezeichnung
IEC 60112 Verfahren zur Bestimmung der Prüfzahl und der Vergleichszahl der Kriechwegbildung von festen, isolierenden Werkstoffen
IEC 60172 Prüfverfahren zur Bestimmung des Tempe-raturindex von Lackdrähten
IEC 60216 Elektroisolierstoffe - Eigenschaften hinsichtlich des thermischen Langzeitverhaltens
IEC 60243 Elektrische Durchschlagfestigkeit von isolierenden Werkstoffen - Prüfverfahren
IEC 60343 Empfohlene Prüfverfahren zur Bestimmung der relativen Beständigkeit isolierender Werkstoffe gegen Durchschlag infolge Oberflächenteilentladung
IEC 60454 Bestimmungen für selbstklebende Isolierbänder für elektrotechnische Anwendungen
IEC 60505 Bewertung und Kennzeichnung von elektrischen Isoliersystemen
IEC 60674 Bestimmung für Kunststoff-Isolierfolienen für elektrotechnische Zwecke
IEC 61234 Prüfverfahren für die Hydrolysebestän-digkeit von Elektroisolierstoffen
IEC 61857 Elektrische Isoliersysteme - Verfahren zur thermischen Bewertung
IEC 61858 Elektrische Isoliersysteme - Thermische Bewertung von Veränderungen an einem erprobten elektrischen Isoliersystem (EIS)
IEC/TS 61934 Elektrische Messung von Teilentladungen (TE) bei sich wiederholenden Spannungsimpulsen mit kurzer Anstiegszeit
IEC 62068 Elektrische Isolierstoffe und Isoliersysteme - Allgemeines Verfahren zur Bewertung der elektrischen Lebensdauer bei Beanspruchung mit sich wiederholenden Spannungsimpulsen
EN 61558 Sicherheit von Transformatoren, Netzgeräten, Drosseln und dergleichen
UL746B Polymerwerkstoffe - Bewertungen der Langzeiteigenschaften
UL 1446 Isoliermaterialsysteme - Allgemein
ASTM D 2275 Prüfung der Spannungsfestigkeit von festen Isolierstoffen unter Einwirkung von Teilentladungen an der Oberfläche
Ökodesign-Richtlinie 2009/125/EG
Über CMC Klebetechnik und die CMC Gruppe
Die CMC Klebetechnik beschichtet seit fünf Jahrzehnten folienartige Materialien mit Klebstoff- und Funktionsbeschichtungen. Auf zwei Beschichtungsanlagen und über 30 Anlagen zur Folienverarbeitung(Formatierer, Stanzanlagen, Rollenschneider) werden hochwertige Folien verarbeitet. Diese werden überwiegend in der Elektrotechnik als Isolationsmaterial eingesetzt, finden aber auch in nahezu allen anderen Industriebereichen Anwendung. Eine große Stärke des Unternehmens ist die Möglichkeit, kundenspezifische Entwicklungen durchzuführen und bedarfsgerecht auch kleinere Chargengrößen anbieten zu können.
1958 Gründung der CMC Klebetechnik GmbH
Zunächst wurde bei dem Tochterunternehmen Colorit GmbH Kohlepapier hergestellt und durch die CMC Klebetechnik vertrieben.
Doch schon bald ergab sich durch die Zusammenarbeit mit der Firma DuPont die Aufgabe, Elektroisolierfolien selbstklebend auszurüsten.
Seit 1962 werden Gewebe, Vliese und Folien beschichtet und danach weiter veredelt.
1995 ISO 9011 Qualitätsmanagement Erstzertifizierung
2001 ISO 14001 Umweltmanagement Erstzertifizierung
2004 Installation einer neuen Beschichtungsanlage für Dispersions- und Lösemittelbeschichtung inklusiv Regenerativer Nachverbrennung
2010 Inbetriebnahme einer Versuchsbeschichtungsanlage in 300mm Breite
2012 Einbindung der Firma CMC Maschinenbau GmbH in den Firmenverbund. Hauptprodukt: Schneid- und Stanzmaschinen für Folienverarbeiter
ab 2006 zunehmend:
Als kleinerer Mittelständler (100 Mitarbeiter) stand nie die Massenproduktion im Vordergrund, sondern stets die auf die Kunden zugeschnittenen Lösungen. Heute erwirtschaftet das Unternehmen deutlich über 50% des Umsatzes durch Produkte, die nur von einem oder wenigen Kunden gekauft werden. Durch die starke Nischenorientierung gibt es eine Vielzahl unterschiedlichster Rezepturen und Anwendungsprofile. Durch dieses breite Fachwissen hat die Anzahl von Lohnbeschichtungen (der Kunde stellt Trägermaterial und/oder Beschichtungsmasse bei) in den letzten Jahren deutlich zugenommen.
Am Standort in Frankenthal / Pfalz arbeiten rund 100 Mitarbeiter in der inhabergeführten CMC-Gruppe (Umsatz > 35 Mio ?). Zur CMC Gruppe gehören neben der CMC Klebetechnik die Colorit GmbH (Produktion, Beschichtung), die Coloprint Tech-Films GmbH & Co. KG (technische Folien, Stanzteile), die CMC Maschinenbau (Stanz- und Schneidanlagen) und die CMC B+V GmbH (Holding). Weitere Standorte und Unternehmen gibt es in Düsseldorf und in Limburgerhof.
Über die Zusendung eines Belegexemplars/Links wären wir dankbar.
---------------------------- English ----------------
For five decades CMC has been coating foil-like materials with adhesive and functional coatings. 150 employees are refining premium films on two coating facilities and over 30 downstream facilities (formatting machines, die-cutting machines, rotative cutting machines). These insulation materials are mainly used in electrical engineering but also across a broad range of industries. The company focuses on the implementation of customer-specific developments as well as professional advice. For more information please visit : www.cmc.de
Themen in diesem Fachartikel:
Unternehmensinformation / Kurzprofil:
Über CMC Klebetechnik und die CMC Gruppe
Die CMC Klebetechnik beschichtet seit fünf Jahrzehnten folienartige Materialien mit Klebstoff- und Funktionsbeschichtungen. Auf zwei Beschichtungsanlagen und über 30 Anlagen zur Folienverarbeitung(Formatierer, Stanzanlagen, Rollenschneider) werden hochwertige Folien verarbeitet. Diese werden überwiegend in der Elektrotechnik als Isolationsmaterial eingesetzt, finden aber auch in nahezu allen anderen Industriebereichen Anwendung. Eine große Stärke des Unternehmens ist die Möglichkeit, kundenspezifische Entwicklungen durchzuführen und bedarfsgerecht auch kleinere Chargengrößen anbieten zu können.
1958 Gründung der CMC Klebetechnik GmbH
Zunächst wurde bei dem Tochterunternehmen Colorit GmbH Kohlepapier hergestellt und durch die CMC Klebetechnik vertrieben.
Doch schon bald ergab sich durch die Zusammenarbeit mit der Firma DuPont die Aufgabe, Elektroisolierfolien selbstklebend auszurüsten.
Seit 1962 werden Gewebe, Vliese und Folien beschichtet und danach weiter veredelt.
1995 ISO 9011 Qualitätsmanagement Erstzertifizierung
2001 ISO 14001 Umweltmanagement Erstzertifizierung
2004 Installation einer neuen Beschichtungsanlage für Dispersions- und Lösemittelbeschichtung inklusiv Regenerativer Nachverbrennung
2010 Inbetriebnahme einer Versuchsbeschichtungsanlage in 300mm Breite
2012 Einbindung der Firma CMC Maschinenbau GmbH in den Firmenverbund. Hauptprodukt: Schneid- und Stanzmaschinen für Folienverarbeiter
ab 2006 zunehmend:
Als kleinerer Mittelständler (100 Mitarbeiter) stand nie die Massenproduktion im Vordergrund, sondern stets die auf die Kunden zugeschnittenen Lösungen. Heute erwirtschaftet das Unternehmen deutlich über 50% des Umsatzes durch Produkte, die nur von einem oder wenigen Kunden gekauft werden. Durch die starke Nischenorientierung gibt es eine Vielzahl unterschiedlichster Rezepturen und Anwendungsprofile. Durch dieses breite Fachwissen hat die Anzahl von Lohnbeschichtungen (der Kunde stellt Trägermaterial und/oder Beschichtungsmasse bei) in den letzten Jahren deutlich zugenommen.
Am Standort in Frankenthal / Pfalz arbeiten rund 100 Mitarbeiter in der inhabergeführten CMC-Gruppe (Umsatz > 35 Mio ?). Zur CMC Gruppe gehören neben der CMC Klebetechnik die Colorit GmbH (Produktion, Beschichtung), die Coloprint Tech-Films GmbH & Co. KG (technische Folien, Stanzteile), die CMC Maschinenbau (Stanz- und Schneidanlagen) und die CMC B+V GmbH (Holding). Weitere Standorte und Unternehmen gibt es in Düsseldorf und in Limburgerhof.
Über die Zusendung eines Belegexemplars/Links wären wir dankbar.
---------------------------- English ----------------
For five decades CMC has been coating foil-like materials with adhesive and functional coatings. 150 employees are refining premium films on two coating facilities and over 30 downstream facilities (formatting machines, die-cutting machines, rotative cutting machines). These insulation materials are mainly used in electrical engineering but also across a broad range of industries. The company focuses on the implementation of customer-specific developments as well as professional advice. For more information please visit : www.cmc.de
Datum: 07.01.2015 - 09:18 Uhr
Sprache: Deutsch
News-ID 1157170
Anzahl Zeichen: 0
Kontakt-Informationen:
Ansprechpartner:
Stadt:
Frankenthal
Telefon:
Kategorie:
Elektro- & Elektronik
Anmerkungen:
Dieser Fachartikel wurde bisher 130 mal aufgerufen.
Der Fachartikel mit dem Titel:
"Versagensgründe für Elektroisolationen"
steht unter der journalistisch-redaktionellen Verantwortung von
CMC Klebetechnik GmbH (Nachricht senden)
Beachten Sie bitte die weiteren Informationen zum Haftungsauschluß (gemäß TMG - TeleMedianGesetz) und dem Datenschutz (gemäß der DSGVO).